
풍력터빈 블레이드 루트부 재료의 음향방출 신호 주파수 특성과 손상 메커니즘 분류에 관한 연구
초록
본 연구는 풍력터빈 블레이드 루트부의 SCM440과 FRP 재료에 대한 음향방출(AE) 신호 특성을 실험적으로 분석하였으며, 인장시험과 AE 측정을 수행하여 각 재료의 기계적 특성, 파괴 거동, AE 신호 특성을 규명하였다. 수집된 AE 데이터를 대상으로 스펙트럴 클러스터링을 적용하여 손상 메커니즘을 체계적으로 분류하고자 하였다. 연구 결과, 두 재료의 고유한 파괴 특성이 AE 신호에 반영되어 재료별 손상 진단의 가능성을 확인하였으며, 각 재료의 미세구조와 파괴 메커니즘에 따른 특징적인 AE 신호 패턴을 식별하였다. 특히 SCM440의 점진적 연성파괴와 FRP의 복합적 취성파괴 과정을 AE 신호의 진폭, 주파수, 클러스터링 분석을 통해 정량적으로 평가함으로써, 풍력터빈 블레이드 루트부의 실시간 건전성 모니터링을 위한 기초 연구 방법론을 제시하였다.
Abstract
This study experimentally analyzed the acoustic emission signal characteristics of SCM440 and fiber reinforced plastic materials in wind turbine blade root sections. Through tensile testing and acoustic emission measurements, we investigated the mechanical properties, fracture behavior, and acoustic emission signal characteristics of each material, aiming to systematically classify damage mechanisms using spectral clustering. The results confirmed the possibility of material-specific damage diagnosis as the unique fracture characteristics of both materials were reflected in the acoustic emission signals, identifying distinctive signal patterns corresponding to each material microstructure and fracture mechanism. Through amplitude, frequency, and clustering analysis of acoustic emission signals, we proposed a fundamental research methodology for real-time health monitoring of wind turbine blade root sections.
Keywords:
Acoustic Emission, Wind Turbine Blade, FRP, SCM440, Clustering키워드:
음향방출, 풍력터빈 블레이드, 클러스터링1. 서 론
풍력발전은 신재생에너지 산업의 핵심 분야로 자리잡으며 지속적인 성장세를 보이고 있다. 특히 발전단가 저감을 위한 대형화 추세가 가속화되면서, 단일 터빈의 용량은 2010년 1.8 MW급에서 현재 15 MW급까지 증가하였다. 이러한 대형화는 블레이드 크기의 증가로 이어져, 최근에는 로터 직경이 130m에 이르는 터빈이 상용화되고 있다.1)
블레이드의 대형화는 발전효율 향상에는 유리하나, 블레이드에 작용하는 하중은 길이에 비례하여 증가하는 특성을 나타낸다.2) 특히 블레이드와 허브를 연결하는 루트부(Fig. 1)는 블레이드에서 발생하는 모든 하중이 집중되는 부위로, 구조적 안전성 확보가 매우 중요하다. 루트부는 복합소재인 블레이드와 금속소재인 허브를 체결하는 이종접합 구조를 가지며, 운전 중 복잡한 하중조건에 노출된다.3,4)
기존의 루트부 건전성 검사는 주로 정기점검 시 육안검사나 초음파 검사 등을 통해 이루어져 왔다. 그러나 이러한 방식은 손상 진행 과정을 실시간으로 파악하기 어렵고, 검사를 위한 터빈 정지가 불가피하다는 한계가 있다.5) 최근에는 가속도계를 이용한 진동 기반 모니터링 기술이 적용되고 있으나, 이는 주로 기어박스나 베어링과 같은 회전체의 결함 진단에 초점이 맞춰져 있다. 또한 진동 신호는 외부 노이즈에 민감하고 재료의 미세 균열과 같은 초기 손상을 감지하기 어렵다는 한계를 갖는다.6)
이러한 한계를 극복하기 위해 음향방출(Acoustic Emission, AE) 기술이 주목받고 있다. AE는 재료 내부의 미세 균열 발생과 진전 시 방출되는 탄성파를 감지하여 손상을 실시간으로 모니터링할 수 있다.7,8) 특히 AE 신호는 손상이 발생하는 순간에만 방출되므로 외부 노이즈의 영향이 적고, 미세 균열이나 손상으로 인한 에너지 방출도 감지할 수 있어 초기 손상 탐지에 유리하다.9) Tang 등은 풍력 터빈 블레이드의 피로 시험에서 AE 기술을 적용하여 손상 진전을 효과적으로 모니터링할 수 있음을 실증한 바 있다.10)
본 연구에서는 블레이드 루트부의 주요 구성 재료인 FRP 복합재료와 실제 허브 체결부에 사용되는 SCM440 강재에 대한 개별 인장시험을 수행하여 AE 신호를 측정하고, 각 재료의 변형단계에 따른 신호 특성을 규명하였다. 특히 AE 신호의 주파수 특성 분석과 스펙트럴 클러스터링(Spectral Clustering) 알고리즘을 적용하여 재료별 손상 메커니즘에 따른 특성 신호를 분류하였다. 이를 통해 루트부를 구성하는 각 재료의 손상 거동을 독립적으로 이해하고, 향후 실제 루트부 건전성 진단을 위한 기초 데이터베이스를 구축하고자 하였다. 또한 파단면 분석을 통해 각 재료의 파괴기구와 AE 신호의 상관관계를 분석하였다.
본 연구의 결과는 풍력발전 블레이드 루트부의 실시간 건전성 모니터링을 위한 기술적 기반을 제공할 것으로 기대된다. 특히 재료별 특성 신호를 분류하고 손상 진행 정도를 정량적으로 평가할 수 있는 방법론을 제시함으로써, 블레이드 루트부의 안전성 향상과 유지보수 효율화에 기여할 수 있을 것이다.
2. 시험편 및 실험 방법
2.1 시험편
본 연구에서는 풍력터빈 블레이드 루트부의 주요 구성 재료인 FRP 복합재료와 허브 체결부 텐션볼트의 적용 소재인 SCM440을 시험 대상으로 선정하였다. FRP는 소규모 시험연구에 적합하고 시중에서 구매가 용이한 FR4 규격의 0°/90° 배열을 가진 2 mm 두께의 판재를 사용하였다. SCM440(C: 0.40%, Si: 0.23%, Mn: 0.73%, P: 0.015%, S: 0.012%, Cu: 0.30%, Ni: 0.05%, Cr: 0.95%, Mo: 0.16%)은 round bar 형태의 소재를 사용하였으며, QT(Quenching and Tempering) 열처리를 통해 요구 물성을 확보하였다. 열처리는 860°C에서 240분간 오스테나이트화 처리 후 60°C 오일 퀜칭하고, 650°C에서 270분간 템퍼링하는 조건으로 수행하였다.
인장시험편은 ASTM 규격11,12)에 따라 제작하였다. SCM440은 ASTM A370 규격의 subsize 시험편으로 게이지 길이 50 mm, 폭 6.25 mm, 두께 6 mm로 가공하였다. FRP는 ASTM D638 Type 1 규격에 따라 게이지 길이 50 mm, 폭 13 mm, 두께 2 mm의 치수로 머시닝 센터를 이용하여 정밀 가공하였다.
2.2 인장시험 중 AE 측정 시험
인장시험은 100 kN 용량의 만능재료시험기를 사용하여 변위제어 모드로 수행하였다. 인장속도는 1.0 mm/min으로 설정하였으며, 하중-변위 데이터는 1,000 Hz의 주기로 획득하였다. 변형률은 크로스헤드 변위를 기반으로 측정하였다.
파단 후 시험편의 파면 분석을 위해 주사전자현미경(SEM) 관찰을 실시하였다. 관찰은 가속전압 30 kV, 작동거리(WD) 25 mm 조건에서 이차전자(SE) 모드로 수행하였다. 이를 통해 파괴 모드와 AE 신호의 상관관계를 분석하였다.
AE 신호 측정은 Vallen Systeme사의 spotWave 시스템을 사용하였다. 본 시스템은 2 MHz의 샘플링 속도를 가지며, 20 kHz 하이패스(2차)와 500 kHz 로우패스(6차) 아날로그 필터, 그리고 Butterworth IIR 디지털 필터를 채용하였다. AE 센서는 100~900 kHz의 주파수 대역을 가진 광대역 센서(VS-900M)를 사용하였으며, 이는 190 kHz와 350 kHz에서 피크 응답을 가진다.
인장 시험 중 시험편의 변형에 따른 AE 신호를 측정하기 위해 AE 센서를 시험편에 설치하였다. 시험편으로부터의 센서 이탈 및 그로 인한 파손 방지를 위해 자체 제작된 홀더를 Fig. 2와 같이 그립부에 장착하였다. 이때 신호 획득의 안정성 확보를 위해 커플런트를 센서 표면에 도포하였다.
AE 센서는 시험편과 직접 면접촉(face contact)하며, 홀더는 시험 중 센서의 안정적 위치 고정을 위해서만 사용되었다. 이 같은 설치 방법은 센서와 시험편 간 음향 방출 신호 전달이 면접촉과 커플런트를 통해 직접적으로 이루어지도록 하여, 신호 품질을 저하시키지 않으면서도 안정적인 측정을 가능하게 한다. AE 신호의 주요 측정 파라미터는 Table 1과 같이 설정하였다.
2.3 클러스터링
AE 신호의 분석을 위해서는 원시 신호로부터 특징을 추출하는 신호 처리 과정이 필수적이다. 신호 처리 과정은 노이즈 제거, 신호 분할, 특징 추출 등을 포함하며, 이는 후속 분석의 신뢰도에 직접적인 영향을 미친다. 본 연구에서 획득된 AE 신호는 다음과 같은 절차로 처리하였다.
- - 인장시험 중 원시 신호 획득
- - Transient 파형 추출 및 노이즈 필터링
- - Short-time Fourier Transform을 통한 주파수 영역 변환
- - Peak frequency와 Peak amplitude 추출
이와 같이 추출된 특징을 기반으로 AE 신호의 클러스터링(군집화)을 진행하였다. 본 연구에서 클러스터링의 목적은 재료의 변형 중 발생하는 서로 다른 손상 기구를 AE 신호의 특성에 기반으로 분류하는 것이다. 클러스터링 분석을 위해 SCM440에서 9,684개, FRP에서 3,536개의 AE 신호를 수집하였으며, 파괴 기구 분류를 위한 주요 특징값으로는 피크 주파수(peak frequency)를 선정하였다.
클러스터링 기법으로는 비선형적 군집 경계 구분이 가능하고 노이즈에 강건한 스펙트럴 클러스터링 기법을 적용하였다. 최적 클러스터 수 결정을 위해 다음의 두 가지 방법을 사용하였다:
엘보우 기법(Elbow method): 클러스터 수에 따른 군집 내 분산의 감소율 분석
실루엣 스코어(Silhouette score): 클러스터 내 응집도와 클러스터 간 분리도의 정량적 평가
3. 결과 및 고찰
3.1 인장시험 및 AE 파라미터
Fig. 3은 FRP와 SCM440 시험편의 응력-변형률 선도와 파단 후 시험편의 외관을 나타낸 것이다. SCM440은 항복강도 735 MPa, 인장강도 868 MPa, 연신율 16%를 나타내었다. 응력-변형률 곡선에서 뚜렷한 항복점과 소성변형 구간이 관찰되었으며, 최대 응력 도달 후 네킹(necking)이 발생하는 전형적인 연성파괴 거동을 보였다. 이는 템퍼링 처리된 마르텐사이트 조직의 특성이 잘 반영된 것으로 판단된다.
반면, FRP는 인장강도 252 MPa, 파단 시 변형률 0.5%로, SCM440 대비 현저히 낮은 연신율을 보였다. 응력-변형률 곡선은 파단까지 거의 선형적인 거동을 보였으며, 뚜렷한 소성변형 없이 급격한 파단이 발생하는 취성파괴 특성을 나타내었다. 일반적으로 이러한 취성파괴는 섬유와 기지(matrix) 간 계면에서의 결합력 부족, 섬유의 파단 또는 기지의 균열 등 복합적인 파괴 기구로부터 기인하는 것으로 알려져 있다.
Fig. 4는 인장시험 후 SCM440 및 FRP 시험편의 파면을 주사전자현미경으로 관찰한 결과를 제시한 것이다. SCM440의 파면에서는 연성파괴의 전형적인 특징인 딤플(dimple) 구조가 관찰되었다. 특히 네킹이 발생한 영역에서는 전단 응력에 의해 연신된(elongated) 딤플도 관찰되었다. 이러한 미세구조는 템퍼드 마르텐사이트의 래스(lath) 구조를 따라 미소공동(microvoid)이 생성되고 성장하여 최종 파단에 이르는 전형적인 연성파괴 메커니즘을 나타내었다.
FRP의 파면에서는 하중 방향에 수직으로 발생한 취성파괴의 특징이 관찰되었다. 파면은 크게 세 가지 주요 파괴 기구의 양상을 나타내었다.
- 1) 기지 균열(matrix crack)
- 2) 섬유 파단(fiber breakage)
- 3) 섬유-기지 계면 박리(delamination)
특히 섬유 파단면이 거의 동일 평면상에 위치한 것은 하중이 급격히 전달되어 순간적인 파괴가 발생했음을 의미한다.
Fig. 5는 각각 SCM440과 FRP의 인장시험 중 측정된 AE 신호의 진폭(amplitude)과 발생률(count rate)을 나타낸 것이다. SCM440의 진폭은 전 변형 구간에서 30~40 dB 범위의 기저 진폭이 지배적으로 관찰되었다. 이는 템퍼드 마르텐사이트 조직에서 발생하는 미세 변형이 비교적 일정한 에너지 수준에서 발생된 것으로 사료된다. 또한 항복점 이전까지 40~50 dB 범위의 저진폭 신호가 간헐적으로 발생하다가, 소성변형 구간에서 50~65 dB 범위의 중진폭 신호 발생이 증가하는 특성을 보였다. 특히 네킹 발생 시점부터는 70 dB 이상의 고진폭 신호가 집중적으로 관측되었으며, 이는 미소공동의 생성과 성장에 따른 것으로 판단된다. 발생률 또한 전 변형 구간에서 일시적인 요동이 관찰되었으나, 일정 범위 내에서 안정적인 값을 유지하였다. 이러한 특성으로부터 SCM440의 연성파괴 과정에서 손상이 점진적이고 안정적으로 진행됨을 확인할 수 있었다.
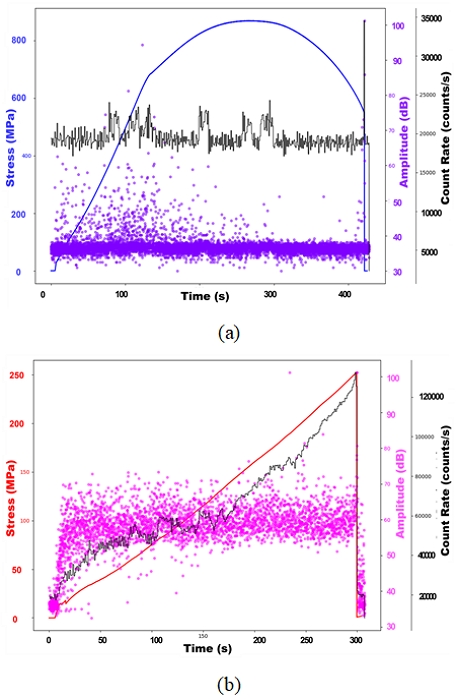
AE amplitude and count rate distribution during tensile loading: (a) SCM440 and (b) FRP superimposed on stress-time curves
반면, FRP는 하중 초기부터 40~80 dB 범위의 다양한 진폭 신호가 관찰되었다. 이는 복합재료의 특성상 하중 초기부터 기지 균열, 섬유-기지 계면 박리 등 다양한 미시적 손상이 복합적으로 발생함을 의미한다. 특히 파단 직전에는 80 dB 이상의 고진폭 신호가 급격히 증가하였는데, 이는 섬유 다발의 급격한 파단에 기인한 것으로 판단된다.
발생률은 하중 증가에 따라 단계적으로 증가하는 경향이 확인되었으며, 이는 하중 증가에 따라 기지 균열, 계면 박리, 섬유 파단 등이 순차적으로 활성화되면서 더 복잡한 AE 신호 특성을 나타낸것으로 판단된다.
3.2 주파수 분석
AE신호 분석에 있어 피크 주파수와 피크 진폭의 상관관계 분석은 재료의 손상 메커니즘을 식별하고 평가하는데 단서를 제공한다. 피크 주파수는 주파수 스펙트럼에서 최대 진폭을 가지는 주파수 성분으로, 결함의 유형과 크기를 반영한다. 피크 진폭은 AE 이벤트의 최대 전압값으로, 손상의 심각도와 에너지 방출 크기를 나타낸다. 이 두 파라미터의 조합 분석을 통해 재료 내부에서 발생하는 손상의 특성과 진행 과정을 평가할 수 있다.
SCM440의 경우(Fig. 6a), 피크 주파수는 주로 100~500 kHz 범위에 걸쳐 넓게 분포하며, 피크 진폭은 30~40 dB 범위의 기저 진폭이 지배적으로 나타났다. 이러한 좁은 주파수 대역의 일정한 진폭 분포는 금속 조직에서 발생하는 미세 변형이 유사한 크기와 특성을 가지고 진행된다고 볼 수 있다. 특히 미소공동의 생성과 성장이 비교적 일정한 에너지 수준으로 방출되는 것으로 판단된다.
반면 FRP는 파괴 기구에 따라 피크 주파수 대역이 다르게 나타난다. 기지 균열(Matrix Cracking)은 80~150 kHz, 층간 박리(Delamination)는 120~300 kHz, 섬유-기지 계면 분리(Fibre/Matrix Debonding)는 170~300 kHz, 섬유 파단(Fibre Breakage)은 250~500 kHz 범위에서 주로 발생하는 것으로 알려져 있다. Fig. 6b에서 관찰할 수 있는 것과 같이 50 kHz와 120 kHz 대역에서 관찰되는 다양한 진폭(40~100 dB) 신호는 각각 기지 파괴와 층간 박리와 관련된 주요한 손상 메커니즘을 나타내며, 이는 FRP의 주요 파괴 특성과 관련한 기존 문헌과 부합하는 결과이다. 300~400 kHz 대역의 저진폭(30~40 dB) 신호는 섬유파단에 기인한 것으로 판단된다.
두 재료의 피크 주파수-진폭 분포 특성을 비교하면, SCM440은 넓은 주파수 대역에서 낮고 균일한 기저 진폭 수준을 유지하는 반면, FRP는 특정 파괴 기구에 따른 좁은 주파수 대역에서 고진폭 신호가 나타나며 다양한 파괴 기구를 동반한다. 이 같은 차이는 연성파괴와 취성파괴의 근본적인 특성을 반영한다고 볼 수 있다. 즉, SCM440의 경우, 미세 균열이나 기공의 점진적 성장과 같은 유사한 크기의 손상이 지속적으로 발생하는 반면, FRP는 기지 균열부터 섬유 파단까지 다양한 크기와 심각도를 갖는 손상이 복합적으로 발생함을 의미한다. 본 연구에서는 광대역 AE 센서를 사용함으로써 이 같은 이종 재료의 특징적인 손상 메커니즘을 효과적으로 구분하고 분석할 수 있었다.
Fig. 7은 FRP 시험편의 인장 시험 각 단계에서 측정된 AE 파형(좌)과 이에 대한 FFT에 의한 주파수 스펙트럼(우)을 나타낸 것이다. 인장 초기(a)에는 진폭이 매우 작고(±0.06 mV) 균일한 연속형 신호가 지배적으로 관찰되었다. 주파수 영역에서 는 100 kHz 이하의 저주파 대역에서 가장 높은 에너지를 보이며, 전체적으로 500 kHz까지 넓게 분포하였다. 이로부터 하중 초기에 발생하는 기지 내 미세균열의 발생과 성장을 추정할 수 있다.
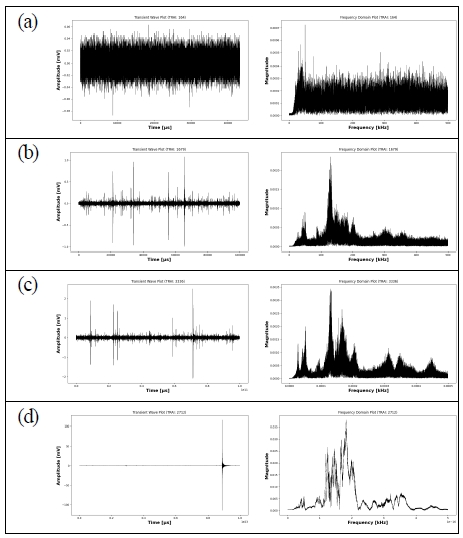
Time domain waveforms (left) and frequency spectra (right) of FRP at different damage stages: (a) initial loading, (b) intermediate loading, (c) near fracture, and (d) final fracture
인장 중기(b)에는 기저 연속형 신호(±0.2 mV)와 함께 ±1.0 mV 수준의 돌발형 신호가 간헐적으로 발생하기 시작하였다. 주파수 스펙트럼에서는 150~200 kHz 대역에서 뚜렷한 피크가 형성되었으며, 이는 섬유-기지 계면 박리와 일부 섬유의 국부적 파단이 시작되었다고 간주할 수 있다.
파단 직전(c)에서는 돌발형 신호의 진폭이 ±2.0 mV까지 증가하고 발생 빈도도 높아졌다. 주파수성분은 더욱 복잡해져 여러 주파수 대역(100 kHz, 150 kHz, 250 kHz, 350 kHz)에서 피크가 관찰되었다. 이는 섬유 다발의 연쇄 파단과 함께 다양한 손상메커니즘이 동시에 활성화되었음을 시사한다.
최종 파단 시(d)에서는 매우 큰 진폭(±100 mV)의 단일 돌발형 신호가 발생하였다. 주파수 스펙트럼은 1~2 kHz 대역에서 높은 에너지 집중을 보였는데, 이는 섬유 다발의 급격한 파단으로 인한 대규모 에너지 방출을 반영한다. 시간에 따른 AE 신호 특성의 변화를 통해 FRP의 점진적인 손상 축적으로부터 최종 취성 파괴에 이르는 과정을 확인할 수 있었다.
Fig. 8은 SCM440 시험편의 인장 시험 각 단계에서 측정된 AE 신호의 시간 영역 파형과 FFT 후 주파수 스펙트럼을 나타낸 것이다. 탄성 구간(a)에 서는 ±0.06 mV 수준의 낮고 균일한 연속형 신호가 관찰되었으며, 주파수 영역에서는 100 kHz 이하의 저주파 대역에서 가장 높은 에너지를 보이며 500 kHz까지 고른 분포를 나타내었다.
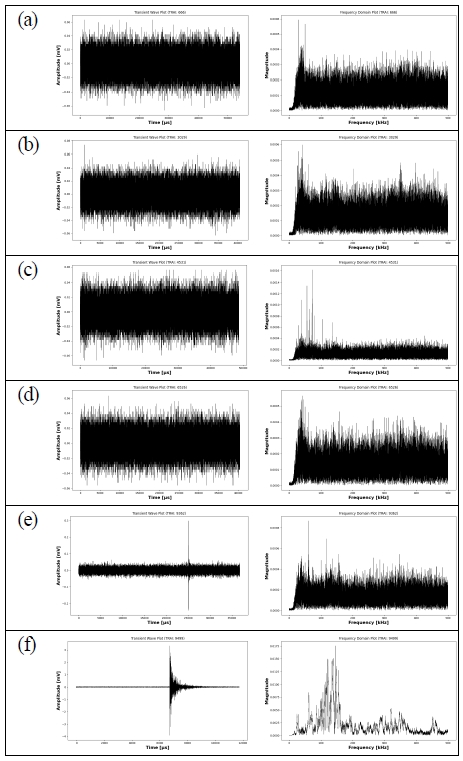
Time domain waveforms (left) and frequency spectra (right) of SCM440 at different deformation stages: (a) elastic region, (b) yielding, (c) plastic deformation, (d) necking, (e) near fracture, and (f) final fracture
항복 구간(b)과 소성 변형 구간(c)에서도 유사한 수준의 연속형 신호가 지속되었다. 주파수 스펙트럼의 전반적인 분포 양상은 유지되었으나, 100~150 kHz 영역에서 다수의 미세한 피크들이 관찰되었다.
Necking 구간(d)에서는 기존의 연속형 신호와 함께 간헐적으로 약간 큰 진폭의 신호가 관찰되기 시작했으며, 이로부터 국부적인 변형이 집중적으로 시작되었다고 추정할 수 있다. 파단 직전(e)에서는 ±0.3 mV 수준의 돌발형 신호가 간헐적으로 발생하였으며, 주파수 스펙트럼에서는 100~150 kHz 영역의 피크가 더욱 뚜렷하게 관찰되었다. 이는 미소공동의 생성과 성장이 더욱 활발해졌음을 시사한다.
최종 파단 시(f)에는 ±2.0 mV 수준의 큰 진폭을 가진 돌발형 신호가 발생하였다. 주파수 스펙트럼은 50~150 kHz 대역에 에너지가 집중되는 특징을 보였는데, 이는 축적된 미소공동의 연결, 균열의 진전 후 최종 파단이 발생했음을 나타낸다.
SCM440과 FRP의 AE 신호 특성을 비교하면, 두 재료의 상이한 미세구조와 파괴 메커니즘이 신호 특성에 명확히 반영됨을 알 수 있다. SCM440은 전 변형 구간에서 비교적 일정한 진폭의 연속형 신호가 지배적이며 파단 직전까지 급격한 변화가 적은 반면, FRP는 하중 증가에 따라 신호의 진폭과 패턴이 단계적으로 변화하며 특히 파단 전에 급격한 변화를 보였다. 진폭 분석 결과, SCM440은 대부분의 변형 구간에서 낮은 진폭을 유지하며 최종 파단 시에도 상대적으로 낮은 진폭을 보이는 반면, FRP는 변형 진행에 따라 진폭이 점진적으로 증가하며 최종 파단 시 매우 큰 진폭을 나타낸다. 주파수 영역 분석 결과, SCM440은 비교적 일정한 주파수 분포를 유지하며 파단 시에도 150 kHz 이하의 제한된 대역에 에너지가 집중되는 반면, FRP는 손상 진행에 따라 주파수 성분이 다양화되며 최종 파단 시 저주파 대역에서 매우 높은 에너지 집중을 보였다. 이러한 특성 차이는 SCM440의 점진적인 연성파괴와 FRP의 복합적이고 급진전적인 취성파괴라는 근본적인 파괴 메커니즘의 차이를 잘 반영한다고 볼 수 있다.
3.3 AE신호 클러스터링
음향방출 신호를 통한 재료의 실시간 건전성 진단을 위해서는 손상 단계별 특성 신호를 효과적으로 분류하는 것이 필수적이다. 특히 블레이드 루트부와 같이 복합적인 하중을 받는 구조물의 경우, 재료의 변형 단계와 균열 발생 등 다양한 손상 메커니즘을 실시간으로 식별할 수 있는 방법론이 요구된다. 본 연구에서는 비지도 학습 기반의 클러스터링 기법을 적용하여 시간-주파수 도메인에서의 AE 신호 패턴 분류를 시도하였다. 이는 실제 운용 환경에서 사전 학습 데이터 없이도 손상을 진단할 수 있는 방법론 개발을 위한 것이다.
본 연구에서는 신호 분류를 위한 특징값으로는 피크 주파수를 선정하였으며, 클러스터링 알고리즘으로는 스펙트럴 클러스터링을 적용하였다. 이는 비선형적이고 수평축에 평행하게 분포하는 신호 그룹들의 특성을 효과적으로 구분할 수 있는 장점이 있다.
본 연구에서는 AE 신호에 대한 최적 클러스터 수 결정을 위해 엘보우 기법과 실루엣 점수를 적용하였다. Fig. 9는 클러스터 수에 따른 두 평가 지표의 변화를 나타낸 것이다. 엘보우 기법은 클러스터 수 증가에 따른 왜곡도(distortion)의 감소율을 분석하는 방법으로, 왜곡도 감소가 급격히 둔화되는 지점(엘보우 포인트)을 최적 클러스터 수로 판단한다. 또한 실루엣 점수는 클러스터 내 데이터의 응집도와 클러스터 간 분리도를 정량적으로 평가하는 지표로, 값이 클수록 클러스터링이 잘 수행되었음을 의미한다.
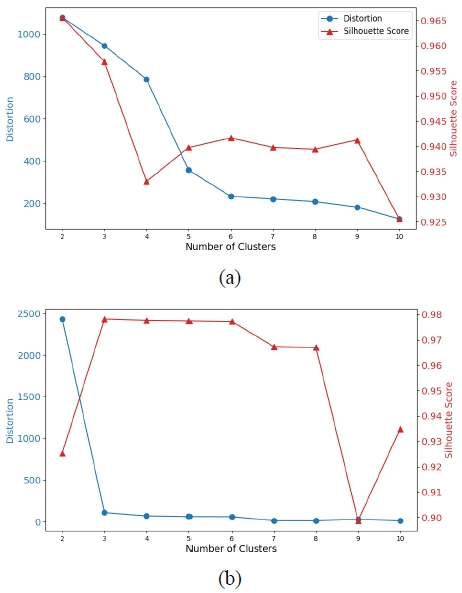
Cluster optimization for AE waveform classification: (a) SCM440 and (b) FRP showing elbow method and silhouette score results
SCM440의 경우, 클러스터 수 5에서 뚜렷한 엘보우 포인트가 관찰되었으며, 실루엣 점수도 이지점에서 최댓값을 보였다. FRP는 클러스터 수 3에서 왜곡도의 감소율이 현저히 감소하고 실루엣 점수가 최대를 나타내어, 이를 최적 클러스터 수로 결정하였다.
Fig. 10은 SCM440 시험편의 AE 신호에 대한 스펙트럴 클러스터링 결과와 K-최근접 이웃(K-nearest neighbors) 알고리즘으로 설정된 결정 경계를 도시하였다. 시간에 따른 피크 주파수 데이터 포인트 분포를 기반으로 클러스터링을 수행한 결과, 5개의 클러스터가 비선형적인 경계를 가지고 분포하는 것으로 확인되었다. K-최근접 이웃 알고리즘은 데이터 포인트 간의 지역적 밀도와 거리를 고려하여 결정 경계를 설정하는데, 이는 SCM440의 연속적인 손상 진행과 클러스터 간 점진적 전이를 효과적으로 특징짓는 것으로 확인되었다. 특히 100~150 kHz대역에서 2개의 주요 클러스터가 형성되었으며, 150~300 kHz 대역에서 3개의 클러스터가 관찰되었다. 클러스터 분포 비율을 살펴보면, cluster 0이 전체의 94.83%로 가장 지배적이며, 이는 템퍼드 마르텐사이트 조직의 안정적인 변형 거동을 반영하는 것으로 사료된다. 나머지 cluster 1(0.4%), cluster 2(2.06%), cluster 3(0.44%), cluster 4(2.27%)는 상대적으로 낮은 비율을 나타내었다. 이는 특정 변형 단계에서 발생하는 미소공동 생성이나 미세균열 진전과 같은 국부적 손상 이벤트를 나타내는 것으로 평가할 수 있다. 특히 K-최근접 이웃 알고리즘으로 설정된 결정 경계는 이러한 소수 클러스터들의 영역을 명확히 구분하면서도, 클러스터 간 전이 영역을 자연스럽게 표현한다고 볼 수 있다.
Fig. 11은 FRP 시험편의 clustering 결과와 SVM(Support Vector Machine) 알고리즘으로 설정된 결정 경계를 나타낸 그래프이다. FRP의 경우, 데이터 포인트들이 시간축에 대해 비교적 수평한 띠 형태로 분포하는 특성이 관찰되었다. 다양한 SVM 커널(선형, RBF, 다항식)을 적용한 결과, 모든 경우에서 뚜렷한 결정 경계가 형성되었으며, 이는 FRP의 각 손상 메커니즘이 주파수 대역에 따라 비교적 명확히 구분됨을 의미한다. 클러스터 분포 비율을 보면, cluster 2가 87.78%로 가장 높은 비율을 차지하며, 이는 기지 내 안정적인 미세균열 진전 단계를 반영한다. Cluster 0은 11.60%로 두 번째로 높은 비율을 나타내었으며, 이는 섬유-기지 계면 박리와 관련된 것으로 판단된다. 특히 선형 SVM의 경우, 2개의 주요 영역으로 단순화된 결정 경계를 나타냈다. 이는 FRP의 손상을 초기 손상(기지 균열, 계면 박리)과 최종 손상(섬유 파단)으로 구분할 수 있음을 시사한다.
이와 같이 클러스터링 분석 결과는 두 재료의 상이한 파괴 기구를 비교적 잘 특징짓는 것으로 확인되었다. SCM440은 템퍼드 마르텐사이트 조직의 점진적 변형 특성으로 인해 클러스터 간 전이가 연속적이고 복잡한 비선형 경계를 보이는 반면, FRP는 기지 균열, 계면 박리, 섬유 파단 등 서로 다른 손상 메커니즘이 단계적으로 발현되면서 뚜렷한 주파수 대역이 구분되었다. 특히 각 재료의 데이터 분포 특성에 적합한 결정 경계 설정 알고리즘을 적용함으로써, SCM440의 연속적 손상 진행과 FRP의 불연속적 파괴 과정을 효과적으로 분류할 수 있었다. 이는 향후 실시간 건전성 진단 시스템 개발에 있어 중요한 기초 자료로 활용될 수 있을 것이다.
4. 결 론
본 연구는 풍력터빈 블레이드 루트부의 주요 구성 재료인 SCM440과 FRP의 음향방출(AE) 신호 특성을 분석하여 각 재료의 손상 메커니즘을 실시간으로 진단하기 위한 기초 연구를 수행하였다.
실험 결과, SCM440과 FRP는 현저히 다른 기계적 특성과 파괴 거동을 보였다. SCM440은 항복강도 735 MPa, 인장강도 868 MPa, 연신율 16%를 나타내며 전형적인 연성파괴 특성을 보였고, 파면 분석에서 딤플 구조와 미소공동 생성이 관찰되었다. 반면 FRP는 인장강도 252 MPa, 파단변형률 0.5%로 취성파괴 특성을 나타냈으며, 기지 균열, 섬유 파단, 섬유-기지 계면 박리 등 복합적인 파괴 기구가 확인되었다.
AE 신호 특성 분석에서도 두 재료의 차이가 뚜렷하게 나타났다. SCM440은 전 변형 구간에서 30~40 dB의 일정한 기저 진폭과 안정적인 신호 발생률을 보였으며, 주파수는 주로 100~500 kHz 대역에 넓게 분포하는 특성을 보였다. 반면 FRP는 40~80 dB의 넓은 진폭 범위를 보였으며, 주파수 특성은 파괴 기구에 따라 특징적인 대역이 관찰되었다.
클러스터링 분석 결과, SCM440은 5개의 클러스터로 분류되어 점진적인 손상 진행 과정을 보였고, FRP는 3개의 클러스터로 구분되어 기지 균열, 계면 박리, 섬유 파단의 단계적 손상 메커니즘이 명확히 구분되었다. 특히 각 재료의 고유한 데이터 분포 특성에 적합한 알고리즘을 적용함으로써 손상 진단의 정확성을 높였다.
본 연구는 풍력터빈 블레이드 루트부의 실시간 건전성 모니터링을 위한 기초 연구로서 의의가 있으나, 실제 운용 환경에서의 검증과 다양한 하중 모드에 대한 추가 연구가 필요하다. 향후 연구에서는 다양한 재료와 하중 조건에서의 AE 신호 특성 분석, 머신러닝 기반 손상 예측 모델 개발, 실제 블레이드 구조물에 대한 적용 연구 등이 수행되어야 할 것이다.
Acknowledgments
본 논문은 교육부와 한국연구재단의 재원으로 지원을 받아 수행된 3단계 산학연협력 선도대학 육성사업(LINC 3.0)의 연구결과입니다.
Author contributions
J. H. Lee; Conceptualization. J. H. Lee; Data curation. J. O. Kwak; Formal analysis. J. H. Lee; Funding acquisition. J. H. Lee; Investigation. S. G. Lee; Methodology. Supervision. S. G. Lee; Validation. J. H. Lee; Writing-original draft. S. G. Lee & J. O. Kwak; Writing-review & editing.
References
-
N. Akhtar, B. Geyer and C. Schrum, 2024, “Larger wind turbines as a solution to reduce environmental impacts”, Scientific Reports, 14(6608), 6608.
[https://doi.org/10.1038/s41598-024-56731-w]
-
Y. Li, X. Liang, A. Cai, L. Zhang, W. Lin and M. Ge, 2023, “Effects of Blade Extension on Power Production and Ultimate Loads of Wind Turbines”, Applied Sciences, 13(6), 3538.
[https://doi.org/10.3390/app13063538]
-
L. M. Jr., 2022, “Root Causes and Mechanisms of Failure of Wind Turbine Blades: Overview”, Materials, 15(9), 2959.
[https://doi.org/10.3390/ma15092959]
-
S. M. Hermansen and E. Lund, 2024, “Multi-material and thickness optimization of a wind turbine blade root section, Structural and Multidisciplinary Optimization”, 67(107), 107.
[https://doi.org/10.1007/s00158-024-03811-0]
-
A. Ghoshal, M. J. Sundaresan, M. J. Schulz and P. F. Pai, 2000, “Structural health monitoring techniques for wind turbine blades”, Journal of Wind Engineering and Industrial Aerodynamics, 85(3), 309-324.
[https://doi.org/10.1016/S0167-6105(99)00132-4]
-
V. Kannan, D. V. Dao and H. Li, 2024, “Detection of Signal Integrity Issues in Vibration Monitoring Using One-Class Support Vector Machine”, Journal of Vibration Engineering and Technologies.
[https://doi.org/10.1007/s42417-024-01435-8]
-
J. J. Lee, D. Y. Cheong, D. H. Park and B. K. Choi, 2023, “Burst Signal Extract and Features Analysis for using Acoustic Emission in Machine Learning”, Journal of Power System Engineering, 27(1), 49-57.
[https://doi.org/10.9726/kspse.2023.27.1.049]
-
K. J. Park, 2021, “Error Analysis for Modal Acoustic Emission Source Localization in Thin Plates”, Journal of Power System Engineering, 25(3), 56-61.
[https://doi.org/10.9726/kspse.2021.25.3.056]
-
Á. Carrasco, F. Méndez, F. Leaman and C. M. Vicuña, 2021, “Short Review of the Use of Acoustic Emissions for Detection and Monitoring of Cracks”, Acoustics Australia, 49(273-280), 273-280.
[https://doi.org/10.1007/s40857-021-00219-4]
-
J. Tang, S. Soua, C. Mares and T. H. Gan, 2017, “A Pattern Recognition Approach to Acoustic Emission Data Originating from Fatigue of Wind Turbine Blades”, Sensors, 17(11), 2507.
[https://doi.org/10.3390/s17112507]
- ASTM A370-21, Standard Test Methods and Definitions for Mechanical Testing of Steel Products, ASTM International, West Conshohocken, PA, 2021.
- ASTM D638-14, Standard Test Method for Tensile Properties of Plastics, ASTM International, West Conshohocken, PA, 2014.