
입열량을 달리한 EH36강 용접재의 기계적 및 침지 특성
Abstract
In this study, shipbuilding grade EH36 steel was welded with different heat input.In order to evaluate the corrosion resistance to acidic and alkaline solutions, it was immersed for 240 hours. In particular, to evaluate the corrosion resistance of the welded specimen by the organic/inorganic hybrid solution, the corrosion resistance of the coated specimen with the curing temperature and curing time was evaluated. In the case of non-coated and non-heat treated specimens, the corrosion resistance of the as-received specimens were better than that of the welded specimens. The welded specimen showed more weight loss by high of heat input. Coated specimen with organic/inorganic hybrid solution showed excellent corrosion resistance at high curing temperature and long time. The acid solution showed a weight loss, but the alkaline solution showed no weight change.
Keywords:
BEH36 Steel, Heat Input, Welding, Mechanical and Immersion Characteristics, Organic/Inorganic Hybrid Solution1. 서 론
3EH36강은 주로 조선 및 오일 플랫폼 용 강종으로 10,000톤 이상인 선체 구조의 제조에 사용될 수 있다. EH36강은 높은 인장 강도를 가지며, 조선 및 오일 플랫폼을 위하여 우수한 인성, 고강도, 내식성, 저온강도 및 인성, 가공 특성 및 용접 특성을 갖는다. Youn 등은 시험편의 크기에 따르는 파괴인성(COD)을 평가하였고,1) 용접부의 피로균열진전 특성평가도 실시하였다.2) Jung 등은 강재의 소성 및 파단 특성을 파단 변형률에 관하여 연구하였다.3) 또한 CO2 용접하여 계장화 압입시험으로 파괴인성을 측정하고, 충격 흡수에너지를 평가하였으며.4) 용접 접합부의 수소 취성 저항 특성도 연구하였다.5) AISI316L과 EH36강의 레이저 용접된 이종 맞대기 용접의 미시조직과 기계적 특성에 대한 용접 속도에 관한 연구도 있다.6) 상기와 같이 다양한 연구가 실시되었지만, 내식성 향상을 위한 유/무기하이브리드 용액에 관한 연구는 저자들에 의하여 연구되었으나,7) 선박용 강판의 용접 입열량에 따른 내식 특성 연구가 필요하다.
본 연구는 선박용 EH36강을 입열량이 다르게 용접하여, 산성 및 알칼리성용액에 240시간 침지하여 내식성을 평가하였다. 특히 유/무기 하이브리드 용액에 의한 용접시험편의 내식성은 경화온도 및 경화시간을 달리하였다.
2. 재료 및 실험방법
재료는 선박용 EH36강(TMCP)이다. 인장시험편은 구입한 상태의 모재시험편, 입열량에 따르는 250A 용접시험편, 300A 용접시험편 및 350A 용접시험편이다. 여기서 용접시험편은 1.4 mm 용가제(세아 DS7100)를 사용하여, 35 cm/min 용접속도로 CO2(FCAW)용접하였다. 용접 조건은 전압 30 V로 일정하게, 전류를 250A, 300A 및 350A로 변화시켰다. 입열량은 (전압×전류× 60)/용접속도에서 각각 12.9 KJ/cm, 15.4 KJ/cm 및 18.0 KJ/cm이다. 재료(EH36강) 및 용접에 사용한 용가제(DS7100)의 기계적 성질 및 화학적 성분을 Table 1과 2에 나타낸다.
인장시험은 만능 인장시험기(Oriental, OTV-10C)를 사용하여, 크로스헤드 속도 2 mm/min으로 실시하였다. 인장시험편은 KS 1호 시험편을 사용하였다. 인장강도와 항복강도는 와이블 해석으로 분포 특성을 평가하였다.
조직은 금속현미경(Olimpus, PME3) 및 전자현미경(Hitachi, S-2700)으로 관찰하였으며, 에칭은 10% 나이탈 용액으로 5초간 실시하였다.
침지시험편은 무코팅 시험편(모재시험편, 250A 용접시험편, 300A 용접시험편 및 350A 용접시험편)과 유/무기하이브리드 용액으로 코팅한 코팅 시험편(모재시험편, 250A 용접시험편, 300A 용접시험편 및 350A 용접시험편)을 사용하였다. 유/무기하이브리드 용액은 우레탄 20 wt.%, SiO2 7 wt.%, 멜라민 3.5 wt.%, 증류수와 알콜을 혼합하였다. 침지시험편은 이소프로판올에서 5분간 초음파세척 후, 건조하였다. 코팅은 5분간 딥 코팅하였으며, 190℃ 및 210℃에서 1, 3, 5분 경화하였다. 산성용액은 6 wt.% 제2염화철수용액과 1 wt.% 염산을 혼합한 것이고, 염기성용액은 NaOH 6 mol/L을 사용하였으며, 시험은 상온에서 100 mL용액 중에 240시간 침지하였다. 표면 상태는 실체현미경 및 외관으로 관찰하였다.
3. 결과 및 고찰
3.1 강도의 와이블 분포 특성
Fig. 1은 본 연구에 사용된 용접 조건을 달리하여, 용접한 시험편의 인장강도와 항복강도를 조사하여 나타낸 것이다. 그림에는 표준편차를 나타내었다. 인장강도는 모재시험편이 평균 526 MPa이고, 250A 용접시험편이 약간 증가하였으나, 300A 및 350A 용접시험편은 감소하였다. 항복강도는 모재시험편이 평균 456 MPa이고, 250A 및 300A 용접시험편이 감소하였으나, 350A 용접시험편은 다시 증가하였다.
인장강도 및 항복강도는 확정치가 아니라 통계적으로 변동하고 있음을 Fig. 1에서 알 수 있었다. 이와 같은 관점에서 해석의 편의성과 최약링크 가설을 고려하여, 아래와 같은 2-파라메터 와이블 분포를 적용하여 와이블 통계 해석을 실시하였다.
(1) |
여기서 α는 확률변수의 변동성을 의미하는 형상파라메터(shape paparmeter)로서 커지면 통계적 분산이 작아지므로 신뢰성이 높아진다. β는 63.2% 확률에서 특성수명을 나타내는 척도파라메터(scale parameter)이다.
Fig. 2(a), (b)는 각각 인장강도와 항복강도를 와이블 확률지에 나타낸 것이다. 인장강도와 항복강도는 와이블 확률분포에 잘 따르고 있음을 알 수 있다. 2-파라메터 와이블 확률 분포 함수의 통계적 특성을 이용하여, 인장 강도에 대한 해석 결과를 Table 3, 4에 나타내었다. Table 3, 4는 산술통계에 의한 평균(Mean), 표준편차(standard deviation, Std) 및 변동계수(coefficient of variation, COV)도 함께 나타내었다.
인장강도의 형상파라메터는 300A 용접시험편 137.5, 모재시험편 116.6, 250A 용접시험편 94.9, 350A 용접시험편 27.3으로 나타났다. 여기서 350A의 형상파라메터가 작게 나타난 것은 과도한 용접 입열에 의하여 인장강도가 분산이 많은 것이 원인이라 판단된다. 이에 따르는 변동계수는 300A 용접시험편 1.0%, 모재시험편 0.9%, 250A 용접시험편 1.2%, 350A 용접시험편 4.0%로 나타났다. 이와 같이 형상계수가 작아짐에 따라서 표준편차가 커지고, 변동계수도 커져서 분산이 많아짐을 알 수 있다. 인장강도의 평균은 250A 용접시험편 > 모재시험편 > 300A 용접시험편 > 350A 용접시험편이었으나, 척도파라메터는 350A 용접시험편 > 모재시험편 > 250A 용접시험편 > 300A 용접시험편이었다. 즉, 350A 용접시험편은 강도의 분산은 많으나, 63.2% 확률의 특성수명이 가장 높게 나타났다.
항복강도의 형상파라메터는 모재시험편 43.2, 250A 용접시험편 40.0으로 비슷하였으며, 300A 용접시험편 28.7, 350A 용접시험편 27.2로 비슷하였다. 이에 따르는 변동계수는 모재시험편 2.7%, 250A 용접시험편 2.9%로 비슷하며, 300A 용접시험편 4.5%, 350A 용접시험편 4.0%로 비슷하였다. 이와 같이 항복강도도 형상계수가 작은 것이 표준편차가 커고, 변동계수도 커서 분산이 많아짐을 알 수 있다. 항복강도의 평균 및 척도파라메터는 모재시험편 > 250A 용접시험편 > 350A 용접시험편 > 300A 용접시험편이었다. 즉, 항복강도의 모재 강도 분산은 가장 적으며, 63.2% 확률에서 특성수명도 가장 높게 나타났다.
3.2 조직 및 파단면 관찰
모재 및 용접부의 조직을 금속현미경을 관찰하여 Fig. 3에 나타내었다. (a)는 모재, (b)는 열영향부, (c)는 용착부를 나타낸다. 모재는 페라이트 조직(흰색)에 소량의 페라이트와 시멘타이트가 층상으로 되어 있는 퍼얼라이트 조직(검은색 또는회색)으로 되어 있음을 확인할 수 있었다. 열영향부는 모재와 동일한 페라이트 조직에 소량의 퍼얼라이트 조직으로 되어 있는 것을 확인할 수 있었다. 또한 모재 조직에 비하여 페라이트와 퍼얼라이트 조직의 크기가 약간 작은 것을 확인할 수 있었다. 이것은 용접 중에 받은 열영향에 의하여 초기 페라이트와 퍼얼라이트 조직이 오스테나이트 조직으로 변태된 후, 냉각 중에 다시 오스테나이트가 페라이트와 퍼얼라이트로 변태될 때, 빠른 냉각 속도에 의하여 결정립의 미세화가 일어났기 때문이라 판단된다. 또한 용착부는 1500℃ 이상에서 용가재와 용융하여 재응고 되어 덴드라이트 조직이 나타나고, 핵생성이 발생한 용가재와 모재가 용융되어 조직이 미세화되었다.
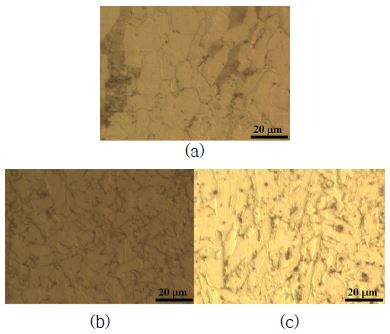
Structure observation by metallurgical microscope. (a) Base metal, (b) HAZ (Heat affected zone), (c) Weld metal
전자현미경에서 얻어진 4종류 시험편의 파단면을 Fig. 4에 나타내었다. (a)는 모재시험편, (b)는 250A 용접시험편, (c)는 300A 용접시험편, (d)는 350A 용접시험편을 나타낸다. 파단면은 연성 파괴의 대표적인 딤플을 나타내고 있다.
3.3 침지 특성
Fig. 5는 무코팅시험편을 산성용액의 침지시험에서 얻어진 외관을 나타낸다. (a)는 모재시험편, (b)는 250A 용점시험편, (c)는 300A 용접시험편, (d)는 350A 용접시험편을 나타낸다. 이 결과에서 침지시간의 증가에 따라서 표면은 광택이 사라지고, 부식에 의하여 표면이 거칠어지는 것을 확인 할 수 있었다. 용접시험편은 용접부의 형상이 뚜렷하게 나타났다.
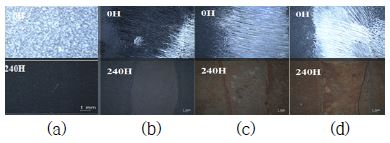
Appearance of 4 kinds of specimen during 240 hour in acidic solution. (a) As-received, (b) 250A weld, (c) 300A weld, (d) 350A weld
Fig. 6은 코팅한 모재시험편을 190℃ 및 210℃에서 1, 3, 5분간 경화 처리 후, 산성용액의 침지시험에서 얻어진 외관을 나타낸다. (a)는 무코팅 모재시험편, (b)는 190℃-1 min 모재시험편, (c)는 190℃-3 min 모재시험편, (d)는 190℃-5 min 모재시험편, (e)는 210℃-1 min 모재시험편, (f)는 210℃-3 min 모재시험편, (g)는 210℃-5 min 모재시험편을 나타낸다. 코팅시험편의 코팅층은 침지시간의 증가에 따라서 박리가 발생하였으나, 무코팅시험편보다는 표면의 거칠음이 적은 것을 알 수 있었다.
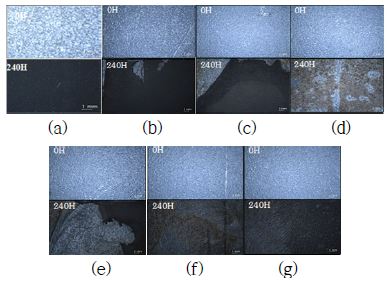
Appearance of as-received coating specimen during 240 hour in acidic solution. (a) Non-coated, (b) 190℃-1 min coating, (c) 190℃-3 min coating, (d) 190℃-5 min coating, (e) 210℃-1 min coating, (f) 210℃-3 min coating, (g) 210℃-5 min coating
Fig. 7 (a), (b)는 각각 산성용액에 침지한 4종류의 미코팅시험편과 열처리 코팅 모재시험편의 무게비와 침지시간의 관계를 나타낸다. (a) 모재시험편의 무게 감소는 가장 작게 나타났으며, 용접시험편은 모재시험편보다 모두 크게 나타났다. 큰 입열량이 무게 감소가 많았다. 용접시험편은 열영향부의 열화 및 조직의 조대화가 산성용액에 부식되기 쉽기 때문이다. (b) 미코팅 모재시험편의 무게 감소는 가장 많이 나타났으며, 열처리 코팅 모재시험편은 미코팅 모재시험편보다 무게 감소가 작았다. 열처리 온도 190℃와 210℃-1 min의 무게 감소는 가장 많았으나, 5 min의 무게 감소는 가장 작았다. 이것은 재료 표면과 코팅층과의 계면 접착력이 양호하였기 때문이다.

Relationship between weight ratio and immersion time in acidic solution. (a) 4 kinds of non-coated specimen, (b) Cured coating as-received specimen
Fig. 8 (a), (b), (c)는 산성용액에 침지한 용접시험편의 무게비와 침지시간의 관계를 나타낸다. (a), (b), (c)는 각각 코팅 250A, 코팅 300A 및 코팅 350A 시험편이다. (a) 미코팅 250A 용접시험편의 무게 감소는 가장 많이 나타났으나, 열처리 용접시험편은 무게 감소가 작았다. 무게감소의 차이는 그렇게 크지 않았다. 무게 감소는 열처리 시간 5분이 가장 작았다. (b) 미코팅 300A 용접시험편의 무게 감소는 가장 많이 나타났으며, 열처리 용접시험편은 무게 감소가 작았다. 열처리 시간 5분의 무게 감소가 가장 작았다. (c) 미코팅 350A 용접시험편의 무게 감소는 가장 많이 나타났으며, 열처리 용접시험편은 무게 감소가 작았다. 열처리 시간 5분의 무게 감소가 가장 작았다. 무게 감소의 경향은 Fig. 7(b)의 모재시험편과 비슷한 경향을 나타내었다.
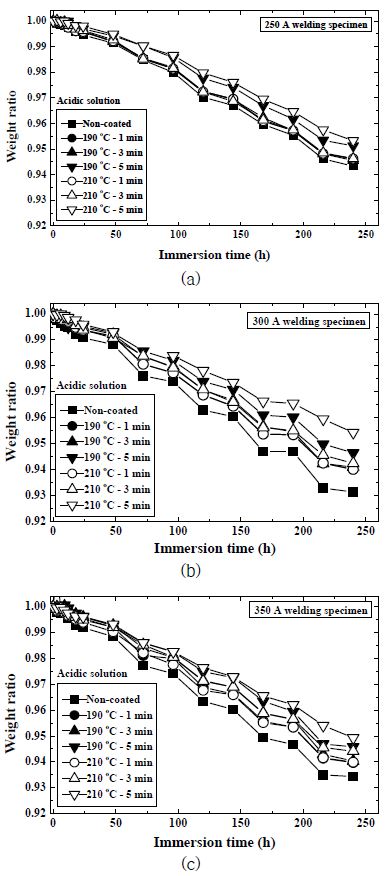
Relationship between weight ratio and immersion time in acidic solution. (a) Coating 250A weld, (b) Coating 300A weld, (c) Coating 350A weld
Fig. 9는 무코팅시험편을 알칼리성용액의 침지시험에서 얻어진 외관을 나타낸다. (a)는 모재시험편, (b)는 250A 용접시험편, (c)는 300A 용접시험편, (d)는 350A 용접시험편을 나타낸다. 이 결과에서 204시간 침지시험편의 표면은 0시간시험편의 표면과 거의 차이가 없었다.
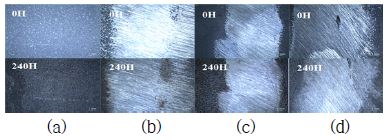
Appearance of 4 kinds of specimen during 240 hour in alkaline solution. (a) As-received, (b) 250A weld, (c) 300A weld, (d) 350A weld
Fig. 10은 코팅한 모재시험편을 190℃ 및 210℃에서 1, 3, 5분간 경화 처리 후, 알칼리성용액의 침지시험에서 얻어진 외관이다. (a)는 무코팅 모재시험편, (b)는 190℃-1 min 모재시험편, (c)는 190℃-3 min 모재시험편, (d)는 190℃-5 min 모재시험편, (e)는 210℃-1 min 모재시험편, (f)는 210℃-3 min 모재시험편, (g)는 210℃-5 min 모재시험편을 나타낸다. 0시간 시험편은 코팅층이 밝게 보이지만, 240시간 시험편은 어두워졌으나 표면 변화는 없었다.
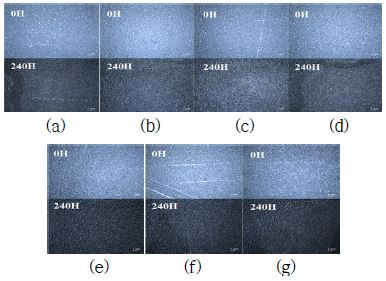
Appearance of as-received coating specimen during 240 hour in alkaline solution. (a) Non-coated, (b) 190℃-1 min coating, (c) 190℃-3 min coating, (d) 190℃-5 min coating, (e) 210℃-1 min coating, (f) 210℃-3 min coating, (g) 210℃-5 min coating
Fig. 11 (a), (b)는 각각 알칼리성용액에 침지한 4종류의 미코팅 모재시험편과 열처리 코팅 모재시험편의 무게비와 침지시간의 관계를 나타낸다. 산성용액의 무게 감소(Fig. 7)는 많이 나타났으나, 알칼리성용액의 무게 감소는 시험편 종류에 관계없이 거의 비슷하였으며, 열처리 온도 및 시간의 영향도 없었다.
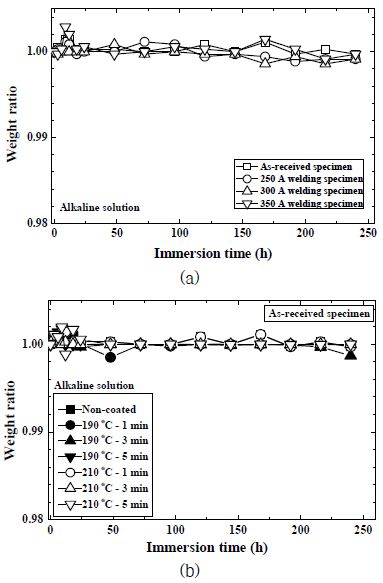
Relationship between weight ratio and immersion time in immersion of alkaline solution. (a) 4 kinds of non-coated specimen, (b) Cured coating as-received specimen
Fig. 12는 4종류의 시험편을 산성용액과 알칼리용액의 침지하여, 얻어진 무게감소비와 경화시간의 관계를 나타낸다. (a), (b), (c)는 각각 경화시간 1분, 3분 및 5분을 나타낸다.
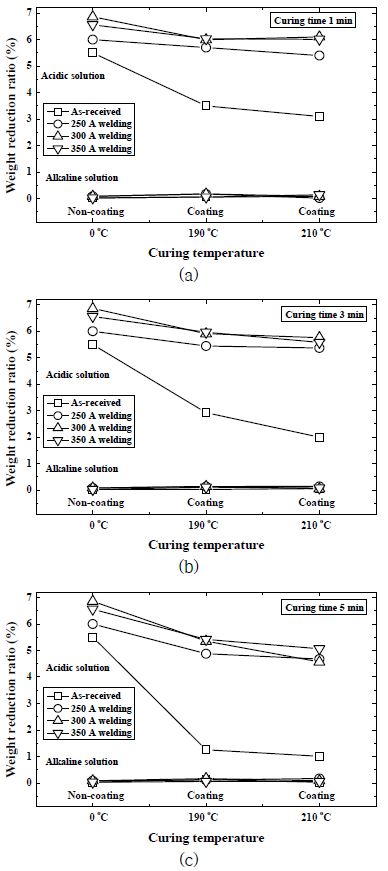
Relationship between weight reduction ratio and curing temperature of 4 kinds of specimen in immersion of acidic solution and alkaline solution. (a) Curing time 1 min, (b) Curing time 3 min, (c) Curing time 5 min
산성용액의 무게감소비는 모재시험편보다 코팅 열처리시험편이 작게 나타났으며, 열처리온도가 높은 것이 약간 더 작게 나타났다. 미열처리 미코팅 모재시험편(□)의 무게감소비가 약 5.5%로 가장 작았다. 미코팅 용접시험편은 250A가 약 6%로 가장 작았으며, 350A(약 6.6%) 및 300A(약 6.9%) 순으로 약간 감소비가 증가하였다. 그리고 코팅 경화 용접시험편은 경화시간 1분(a)과 3부(b)에서 190℃와 210℃의 감소비는 비슷하였으나, 경화 시간 5분(c)는 190℃보다 210℃의 무게감소비가 약간 작았다. 구체적으로 살펴보면, 경화시간 1분(a)의 코팅 190℃ 열처리시험편은 모재시험편 약 3.5%, 250A 용접시험편 약 5.7%, 300A 용접시험편 약 6.0% 및 350A 용접시험편 약 6.0%를 나타내었다. 한편 코팅 210℃ 열처리시험편은 모재시험편 약 3.1%, 250A 용접시험편 약 5.4%, 300A 용접시험편 약 6.1% 및 350A 용접시험편 약 6%를 나타내었다. 경화시간 3분(b)의 코팅 190℃ 열처리시험편은 모재시험편 약 3.0%, 250A 용접시험편 약 5.4%, 300A 용접시험편 약 5.9% 및 350A 용접시험편 약 6.0%를 나타내었다. 한편 코팅 210℃ 열처리시험편은 모재시험편 약 2.0%, 250A 용접시험편 약 5.4%, 300A 용접시험편 약 5.7% 및 350A 용접시험편 약 5.6%를 나타내었다. 경화시간 5분(c)의 코팅 190℃ 열처리시험편은 모재시험편 약 1.3%, 250A 용접시험편 약 4.9%, 300A 용접시험편 약 5.3% 및 350A 용접시험편 약 5.4%를 나타내었다. 한편 코팅 210℃ 열처리시험편은 모재시험편 약 1.0%, 250A 용접시험편 약 4.7%, 300A 용접시험편 약 4.6% 및 350A 용접시험편 약 5.1%를 나타내었다. 이와 같이 미코팅 미열처리 모재시험편은 용접시험편의 무게 감소가 미용접시험편보다 많이 나타났다. 그러나 코팅 열처리시험편은 모재시험편의 무게감소비가 작았으며, 열처리 온도가 높은 것이 더 작게 나타났다. 용접시험편은 3종류가 비슷하였으나, 210℃- 5분 열처리 300A 용접시험편의 무게 감소가 근소한 차이지만, 가장 작게 나타났다.
한편 알칼리성용액에서 모재시험편 및 용접시험편의 무게감소비는 코팅 및 열처리에 관계없이 거의 변화가 없는 것으로 나타났다. 즉 알칼리성용액에서는 부식반응이 일어나지 않는 것으로 판단된다.
철(Fe)은 산소가 용존된 물과 반응하여 수산화철로 부식된다. 그러나 염소이온이 존재하면 부식속도는 매우 빠르다. 본 연구에 사용한 산성용액은 염소이온을 가지고 있으므로, 산성용액에서 EH36강은 부식이 발생하였다. 이러한 부식 반응은 다음과 같이 나타낼 수 있다.8)
(2) |
(3) |
(4) |
전반적인 부식은 식 (2)로 나타내지만, 부식 초기는 식 (3)과 같이 철은 제1철염화수산화물로 산화되면서 수소가 발생한다. 다음으로 식 (4)와 같이 제1철수산화물이 수소 및 산소와 반응하여, 제2철수산화물로 산화되면서 염소이온과 수소이온이 발생한다.
이와 같이 코팅시험편의 무게감소가 작은 것은 하이브리드로 유/무기 물질은 정교한 분자 가교를 형성하여, 고강도 코팅층을 만든다.9)
따라서 본 연구에 적용한 유/무기하이브리드 용액을 혼합하여, EH36강의 1 도장재로 사용하면 내식성 향상에 기여할 것으로 판단된다.
5. 결 론
본 연구는 선박용 EH36강을 입열량이 다르게 용접을 실시하였다. 산성 및 알칼리성용액에 대한 내식성을 평가하기 위하여, 240시간 침지하였다. 특히 유/무기 하이브리드 용액에 의한 용접시험편의 내식성을 평가하기 위하여, 코팅시험편의 경화온도 및 경화시간에 따른 내식성을 평가하였다. 얻어진 결론은 다음과 같다.
1) 미코팅 미열처리한 시험편은 모재시험편이 용접시험편보다 내식성이 우수하였으며, 용접시험편은 입열량이 많을수록 무게 감소가 많았다.
2) 유/무기 하이브리드 용액으로 코팅한 시험편은 경화온도가 높고, 시간이 길수록 우수한 내식성을 나타내었다.
3) 산성용액은 염소이온과 수소이온이 산화피막을 쉽게 파괴하므로 부식의 촉매역활을 하므로 무게감소가 나타났다. 그러나 알칼리성용액은 무게변화가 없었다.
4) 본 연구에 적용한 유/무기 하이브리드 용액은 염소이온과 수소이온의 발생을 차단할 수 있으므로, 도장재의 부식방지 억제제로 사용할 수 있다.
References
- J. G. Youn, D. H. Kim, S. H. Hwang, and M. I. Kim, (1984), "The Effect of Specimen Size on Fracture Toughness (COD) of ABS EH 36 Steel", Journal of the Korean Institute of Metals, Vol. 22(No. 11), p1077-1083.
-
L. W. Tsay, T. S. Chern, C. Y. Gau, and J. R. Yang, (1999), "Microstructures and Fatigue Crack Growth of EH36 TMCP Steel Weldments", International Journal of Fatigue, Vol. 21(No. 8), p857-864.
[https://doi.org/10.1016/s0142-1123(99)00021-3]
-
J. Choung, C. S. Shim, and K. S. Kim, (2011), "Plasticity and Fracture Behaviors of Marine Structural Steel, Part III: Experimental Study on Failure Strain", Journal of Ocean Engineering and Technology, Vol. 25(No. 3), p53-66.
[https://doi.org/10.5574/KSOE.2011.25.3.053]
-
G. N. Kim, J. S. Lee, J. H. Hyeon, Y. G. Jung, and S. C. Huh, (2014), "Evaluation of Low Temperature Properties in EH36 Thick Steel Plate Welded Material by Instrumented Indentation Equipment", Journal of the Korean Society for Power System Engineering, Vol. 18(No. 4), p104-111.
[https://doi.org/10.9726/kspse.2014.18.4.104]
-
S. H. Wang, W. C. Luu, K. F. Ho, and J, K. Wu, (2003), "Hydrogen Permeation in a Submerged Arc Weldment of TMCP Steel", Materials Chemistry and Physics, Vol. 77(No. 2), p447-454.
[https://doi.org/10.1016/s0254-0584(02)00100-1]
-
L. Cao, X. Shao, P. Jiang, Q. Zhou, Y. Rong, S. Geng, and G. Mi, (2017), "Effects of Welding Speed on Microstructure and Mechanical Property of Fiber Laser Welded Dissimilar Butt Joints between AISI316L and EH36", Metals, Vol. 7(No. 7), p270-283.
[https://doi.org/10.3390/met7070270]
-
Ki-Woo Nam, and Kwang-Ho Lee, (2017), "Corrosion Resistance of SPCC, SPFC590, SPFC780 Steel by Organic/Inorganic Hybrid Solution (Case of different SiO2 Polysilicate under a Constant Melamin)", Journal of the Korean Society for Power System Engineering, Vol. 21(No. 2), p5-13.
[https://doi.org/10.9726/kspse.2017.21.2.005]
- D. S. Ahn, (1997), "A new corrosion mechanism of iron in chlorine contaminated solutions", Proceeding of The Korean Institute of Surface Engineering 1997 Spring Annual Meeting, p115.
- S. Yamasaki, S. Tanaka, M. Fukuda, Y. Murayama, Y. Kondo, H. Ogasawara, and O. Uchida, (2010), "Development of the Organic-inorganic Hybrid Super-hydrophilic Layer", Fujifilm Research & Development, No. 55, p29-32.