
열풍 및 동결 건조용 하이브리드 히트펌프 시스템 개발
초록
건조 공정의 에너지 및 이산화탄소 배출량을 저감하기 위한 대체 공정으로 고효율 에너지 기기인 히트펌프가 주목받고 있다. 건조공정에 히트펌프가 적용되면 기존 보일러를 사용할 때와 비교하여 에너지 소비율 및 탄소배출량을 효과적으로 감소시킬 수 있을 뿐 아니라, 열풍건조 및 동결건조를 한 개의 건조기 시스템에서 수행될 수 있다. 본 연구에서는 열풍 및 동결 건조 하이브리드 히트펌프 시스템을 설계하고 실제로 제작하였다. 제안된 시스템의 최적 냉매를 선정하기 위해 세 가지 다른 냉매를 적용한 사이클 시뮬레이션 및 성능계수 비교 연구를 수행하였고, 성능계수 비교를 통해 R134a가 제안된 시스템에 최적 냉매인 것을 확인하였다. 설계 연구를 통해 도출된 데이터를 바탕으로 실제 시스템을 제작하였고 실험 연구를 통해 시스템 안정성 및 건조기 내부 목표온도 도달 시간을 평가하였다. 각 모드가 순차적으로 변화하는 운전모드를 실험적으로 평가하여 제작된 시스템의 시스템 안정성을 확인하였으며, 열풍 및 동결 건조 목표 온도에 도달하는 시간이 각각 65분 그리고 45분이 소요됨을 확인하였다.
Abstract
The heat pump process is attracting attention as an alternative high-efficiency energy device to reduce energy consumption and carbon emission of the drying process. In addition, the application of the heat pump as an energy supply system for dryer system also can perform the hot air drying and the freeze drying processes in one dryer system. This research focuses on the design and development of the hybrid freeze-hot air drying system based on a heat pump. The cycle simulations were performed with three different refrigerants to select the optimal refrigerant and the R134a was selected as the optimal refrigerant through the comparison of coefficient of performance (COP). The current suggested hybrid freeze-hot air drying system based on a heat pump was actually manufactured in this study. In addition, the system stability and time to reach the target temperature in the drying chamber were examined by experimental study. The system stability of the developed system was confirmed by the variation of inner chamber temperature and inlet and outlet temperature of compressor according to the sequentially changed operation modes. In addition, the time to reach target temperature for the heating and cooling operating mode was 65 and 45 minutes, respectively.
Keywords:
Dryer, Hot Air, Freeze, Heat Pump, Cycle Simulation키워드:
건조기, 열풍, 동결, 히트펌프, 사이클 시뮬레이션1. 서 론
급격한 기후변화와 이상고온 현상으로 인해 기온, 습도, 강수량 등의 변화를 야기하고 있으며, 이는 인류의 관련된 모든 분야에 다양하면서 광범위한 영향을 가져다 줄 수 있고, 특히 자연 건조방식을 많이 택하고 있는 우리나라의 농수산물 건조 식품의 생산량 저감 및 품질저하 등과 같은 피해를 유발하고 있다. 또한 미세먼지 고농도 사례가 증가함에 따라 야외 자연 건조 식품들의 위생안정성과 같은 문제 역시 야기되고 있다.
우리나라의 대표적인 건조식품인 곶감, 황태, 오징어 등을 생산하는 전통 건조법인 겨울철 동건법은 피 건조물을 겨울철의 낮과 밤의 온도차를 이용해서 냉동과 해동이 반복적으로 일어나며 피 건조물의 독특한 조직감과 향기를 갖게 하는 전통 건조법이다. 하지만 급격한 기후변화와 이상고온 현상 그리고 미세먼지 고농도화 등의 문제로 인해 건조식품 생산업계에서는 생산량 저감, 풍미(맛) 저감, 식품 위생성 저감 등 다양한 피해를 호소하고 있는 상황이다. 특히 동건법을 포함하는 자연 건조법의 경우, 대부분 옥외 건조장에서 건조 생산되기 때문에 황산염, 질산염 등의 이온 성분과 금속 산화물, 탄소화합물 등의 유해물질이 주성분인 미세먼지 농도가 높아지게 되면 생산되는 건조식품의 위생안정성에 심각한 타격을 준다. 따라서 업계에서는 겨울철 동건법을 포함하는 자연 건조 방식을 미세먼지를 차폐할 수 있는 공간에서 모사할 수 있는 건조 시스템 개발에 관심이 높다.1)
기존 건조 시스템은 화석연료를 기반으로 하는 산업용 보일러를 이용하는 에너지 다소비 기기를 사용하는 시스템으로 높은 소비 에너지가 요구되며 탄소배출량 역시 높다. 따라서 최근에는 급격한 기후변화와 이상고온현상의 원인이 되는 온실가스 배출량 저감과 에너지 고효율 기기로의 전환 등의 이슈를 만족시킬 수 있는 기술 수요가 증가하고 있다. 최근 대표적인 고효율 차세대 열원기기로 히트펌프가 주목받고 있으며, 건조 산업에 산업용 보일러를 대체하게 되면 높은 에너지 절감 및 탄소배출량 저감을 달성할 것으로 기대된다.2)
히트펌프의 경우, 응축기의 고온 열원 그리고 증발기의 저온 열원을 동시에 활용할 수 있으며, 사이클 압력을 조절하여 건조 온도 제어가 가능한 장점이 있다.3-9) 여러 가지 건조기 구동 방법 중 열풍 건조기는 대류 전열 건조라고도 하며, 열풍과 재료를 직접 접촉시켜서 열을 전달하고, 수분을 증발시키는 방식이다. 주로 통기식 건조기 및 공기 부양식 건조기에 사용되는 건조방식으로 국내 건조기의 90% 이상을 점유하고 있으며, 보통 열풍 건조의 경우, 건조 후 열풍을 외부로 배출하고 새로운 외기를 다시 가열하여 건조기 내부로 유입시키기 때문에 에너지 손실이 큰 단점이 있다. 동결 건조의 경우, 물의 비등점아래 온도까지 피 건조물을 냉동시켜 동결 고체화시키고 동결된 수분인 얼음을 바로 기체로 승화시켜 수분을 제거하는 방식으로 다른 건조 방법보다 피 건조물의 열 변형과 향미 그리고 영양보존 면에서 우수하지만 초기 투자비 및 운영비가 높고 건조시간이 오래 소요되는 단점이 있다. 이에 반해 히트펌프를 활용한 건조방식의 경우, 고온의 응축열과 저온의 증발열을 동시에 활용이 가능함에 따라 열풍 건조와 동결 건조를 하이브리드 방식으로 운전이 가능하고 건조시간 단축과 건조효율 향상이 가능한 건조방식이다.
최근 차세대 산업용 대체 열원기기 관련 연구동향을 보면 기존 열원기기를 히트펌프로 대체하는 연구들이 진행 중에 있다.10-15) 하지만 히트펌프를 적용하고 열풍과 동결 건조가 가능한 열풍 및 동결 건조용 하이브리드 히트펌프 시스템 개발 연구는 배관구성의 복잡함과 사방밸브의 내구성 문제 등으로 인해 연구개발이 미진한 상태이다.
따라서 본 연구는 급격한 기후변화와 이상 고온현상 그리고 미세먼지 고농도 사례 등의 피해를 겪고 있는 국내 자연 건조 산업이 당면한 문제를 해결할 수 있는 고효율 열풍 및 동결 건조용 하이브리드 히트펌프 시스템을 개발하고 성능평가를 수행하였다.
2. 연구방법
Fig. 1은 본 연구에서 개발된 열풍 및 동결 건조용 하이브리드 히트펌프 시스템의 사이클 배관 구성 및 운전 흐름도를 나타낸 것이다. 본 연구에서는 단일 히트펌프 사이클에서 온도 상승 운전과 건조 운전 그리고 냉각 운전이 가능하도록 사방 밸브 (4-way valve)와 전자밸브를 사용하여 운전모드가 바뀔 때 냉매의 방향을 유동적으로 변화하도록 사이클을 설계하였다. 그리고 체크밸브를 사용하여 운전모드 전환 시에 냉매의 압력으로 개폐되어 팽창밸브로 유입되도록 하였다. 온도상승 운전 모드 (Fig. 1 (a))는 건조기의 초기 운전 시 건조 챔버 내부를 목표 온도까지 빠르게 상승시키기 위해 외부 열교환기(SUB H/X)가 증발기 역할을 수행하며, 챔버 내부의 응축기가 순환공기의 온도를 상승시켜 건조 챔버 내부의 온도를 빠르게 상승시킨다. 건조 운전모드(Fig.1 (b))는 건조 챔버 내부가 목표온도까지 도달하였을 때 피 건조물을 건조하기 위한 모드로 챔버 내부의 응축기는 압축기에서 토출된 고온의 냉매와 열 교환으로 열풍을 공급하고, 내부 증발기는 높은 습도의 공기를 노점온도까지 낮추어 수분을 응축시키는 역할을 수행한다. 그리고 외부 열교환기는 내부 응축기의 냉매 응축부하를 보조한다. 냉각 운전모드(Fig.1 (c))는 피 건조물이 목표 함수율까지 열풍 건조가 완료된 후 동결 건조를 위한 모드로 챔버 내부의 증발기에서 저온의 냉매와 순환 공기의 열 교환으로 건조 챔버의 온도를 낮추고 외부 열교환기가 압축기에서 토출된 고온의 냉매를 응축시키는 역할을 수행한다.
본 연구에서 제안하는 열풍 및 동결 건조용 하이브리드 히트펌프 시스템의 최적 냉매를 결정하기 위해 R134a, R404A 그리고 R410A 냉매를 후보군으로 하여 사이클 시뮬레이션을 수행하였으며, 이는 상용프로그램인 하이시스(Aspen HYSYS)를 통해 수행되었다. 세 가지 냉매를 적용했을 때, 제안된 시스템의 온도 상승모드, 건조 운전 모드 그리고 냉각 운전 시 공기유입 유량, 응축기와 증발기의 열량 그리고 압축기 소모 에너지 등을 산출하였고, 최종적으로는 성능계수(Coefficient Of Performance, COP)를 분석하여 최적냉매를 선정하였다.
Fig. 2는 본 연구에서 개발된 열풍 및 동결 하이브리드 히트펌프 건조기의 실물 사진과 요소부품의 사진을 나타낸 것이다. 사이클 시뮬레이션 결과를 통해 얻은 최적 냉매(R134a)를 적용하였으며, 압축기는 Copeland사의 5 kW급 ZS11KAE Model을 선정하고 인버터를 사용하여 사이클 압력제어가 가능하도록 설계, 제작하였다. 팽창밸브는 최대 용량 5 kW를 기준으로 Danfoss사의 EEV ETS 6-14를 사용하였으며, 건조 챔버 내부의 증발기와 응축기 그리고 외부 열교환기의 세부정보는 Table 1부터 3에 나타내었다.
3. 결과 및 논의
3.1 냉매 별 사이클 시뮬레이션
Table 4는 세 가지 냉매를 적용한 열풍 및 동결 건조용 하이브리드 히트펌프 시스템의 온도상승 모드 시뮬레이션 결과이다. 건조기 내부 목표 온도는 50℃이다. 겨울철 동건법을 모사할 수 있는 시스템을 설계하고자 하였기 때문에 증발기 온도는 -10℃로 고정하여 시스템을 구성하였다. 세 가지 냉매를 적용하여 온도 상승 모드 사이클을 구성하였을 때, R134a가 2.444로 COPH가 가장 높음을 알 수 있었다. 압축비는 R134a가 7.48로 가장 높았으나 응축기 내부 압력이 다른 냉매들 보다는 낮아 압축기 일이 낮기 때문 상대적으로 높은 COPH를 나타내었다.
Table 5는 세 가지 냉매를 적용한 열풍 및 동결 건조용 하이브리드 히트펌프 시스템의 건조 운전 모드 시뮬레이션 결과이다. 본 연구에서는 건조기 내부의 피 건조물에서 나오는 수분 응축에 대한 고려를 하지 않았으며, 건조기 내부의 온도가 50℃로 유지될 수 있도록 시스템 시뮬레이션을 수행하였다. 이때 증발기의 열량이 내부 응축기 열량보다 높기 때문에 열량 균형을 맞추기 위해 외부 응축기(Sub. Cond.)를 두었다. R134a, R404A 그리고 R410A 세 가지 냉매를 적용하여 건조 운전 모드 사이클을 구성하였을 때 온도 상승 운전 모드와 마찬가지로 압축일이 가장 낮은 R134a가 COPH 1.444로 가장 높은 값을 나타내었다.
Table 6는 세 가지 냉매를 적용한 히트펌프 하이브리드 동결 및 열풍 건조기 냉각 운전 모드 시뮬레이션 결과이다. 겨울철에도 냉각 운전모드를 적용할 수 있도록 증발기 온도를 -13℃로 고정하였으며, 건조기 내부의 온도를 -5℃로 설정하였다. 시뮬레이션 결과, 다른 운전모드와 같은 이유로 R134a를 적용하였을 때 COPC가 1.957로 가장 높음을 알 수 있었다.
세 가지 다른 냉매를 적용하여 열풍 및 동결 건조용 하이브리드 히트펌프 시스템의 사이클 시뮬레이션을 수행하였을 때 R134a가 세 가지 모드에서 모두 가장 높은 COPH&C를 달성하였고, 최적 냉매로 선정되었다.
3.2 시스템 안정성 및 목표 온도 도달 시간 평가
세 가지 냉매를 적용한 열풍 및 동결 건조용 하이브리드 히트펌프 시스템 시뮬레이션을 통해 적용될 수 있는 최적 냉매를 R134a로 결정하였고, 이를 적용하여 제안된 시스템을 제작하였다. 개발된 제품의 실제 운전에서 발생할 수 있는 문제점을 확인하고 보완하고 자 사전 실험 연구를 수행하였다. 사전 실험 연구를 위해 온도 상승 운전모드와 냉각 운전 모드의 목표온도를 각각 25℃ 그리고 -5℃로 하고 운전 모드를 변화시켜 가며 건조기 내부 온도의 변화와 그 추이를 파악하였다.
본 실험을 위해 Table 4와 6에 나타낸 온도상승운전모드와 냉각운전모드의 사이클 조건을 활용하였다. Fig. 3에서 볼 수 있듯이, 실험은 각 모드별로 3회씩 진행되었으며, 온도 상승 운전을 했을 때 평균적으로 13분 정도면 목표 도달 온도인 25℃에 도달할 수 있음을 알 수 있었다.
냉각 운전을 했을 때, 건조기 내부의 온도가 25℃에서 -5℃까지 도달하는데 약 12.3분이 소요되는 것을 알 수 있었다. 온도 상승 운전모드에서는 건조기 내부의 온도가 선형적으로 증가하는 것을 알 수 있었다. 냉각 운전 모드에서는 냉각 운전 모드 시작 후에 약 2분 동안 평균적으로 약 17℃가 급격히 감소함을 알 수 있었으며, 이후 건조기 내부의 온도가 선형적으로 감소함을 알 수 있었다. 건조기 내부의 온도변화는 온도상승운전모드에 비해 냉각운전모드의 경우가 초기에 급격한 변화를 보여 주는데, 이는 압축기의 압축은 선형적으로 이루어지지만, 팽창은 순식간에 일어나기 때문이다.
하지만 냉각운전모드 구동 시에 약 2분 후에 온도변화가 완만해지는 것을 볼 수 있으며, 이는 저온으로 내려갈수록 건조기 내부의 온도가 외부의 열 유입에 더 큰 영향을 받기 때문인 것으로 파악된다. 또한 본 테스트를 통해 개발된 건조기의 온도 상승 모드와 냉각 운전 모드가 제작된 시스템 내에서 문제없이 잘 이루어짐을 확인할 수 있었다.
Fig. 4는 순차적으로 변화하는 운전모드에 따른 (a) 건조기 내부 온도변화 및 (b) 압축기 입구 및 출구 온도변화를 나타낸 그래프이다. 건조 운전 모드 시 건조기 목표 내부 온도가 50℃이고 냉각 운전 모드 시 건조기 목표 내부 온도가 -5℃이다.
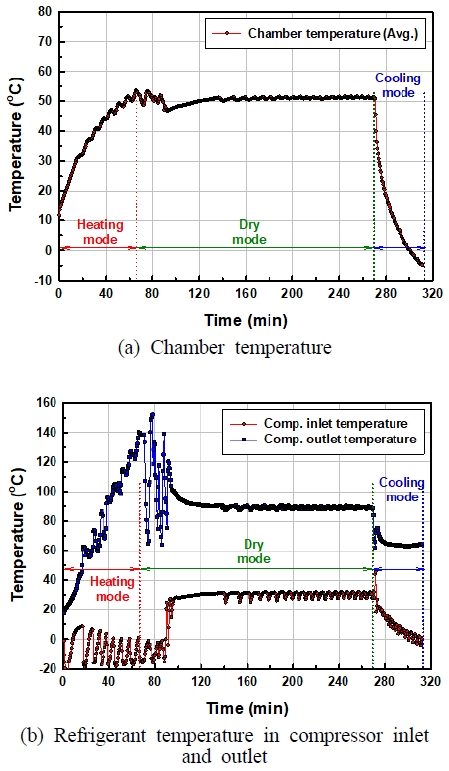
Variation of chamber temperature and inlet and outlet refrigerant temperature in compressor according to the time
상온 10℃에서 온도 상승 운전 모드를 가동하여 건조기 내부 온도를 50℃까지 올리는데 걸린 시간은 약 65분이었다. 건조기 내부 온도가 30℃까지는 시간에 따라 선형적으로 증가하였으나 이후 50℃까지는 점근적으로 증가함을 알 수 있었는데, 이는 건조기 목표 내부온도를 맞추기 위해압축기 구동이 제어되었기 때문이다.
온도 상승 모드 후 건조 운전 모드로 전환하여 건조기 내부 온도를 50℃로 약 200분 동안 유지하였으며, 이때 건조기 내부 온도가 매우 안정적인 것을 알 수 있다. 이후 건조 운전 모드에서 냉각 운전 모드로 전환하여 건조기 내부 온도를 -5℃까지 안정적으로 냉각하였고, 약 45분 정도가 소요됨을 알 수 있었다.
운전 모드 변화에 따른 건조기 내부 온도 변화 및 압축기 입/출구 온도 변화로 보아 제작된 시스템이 안정적으로 잘 작동함을 알 수 있었다.
4. 결 론
본 연구를 통해 온도상승운전, 건조운전, 그리고 냉각 운전모드가 하나의 히트펌프 시스템을 통해 구현될 수 있는 열풍 및 동결 건조용 하이브리드 히트펌프 시스템을 설계 및 제작하였다. 이를 위해 세 가지 서로 다른 냉매를 선정하여 이를 적용한 시스템을 사이클 시뮬레이션을 통해 분석하고 최적 냉매를 선정하였다. 선정된 냉매를 적용한 실제 열풍 및 동결 건조용 하이브리드 히트펌프 시스템을 제작하였고, 실제 구동 실험을 통해 시스템 안정성 및 건조기 내부 목표 온도 도달 시간을 측정하였으며, 결과는 다음과 같다.
1) R134a, R404A 그리고 R410A를 냉매 후보군으로 선정하여 Aspen Plus HYSYS 프로그램을 통해 온도 상승 운전모드, 건조 운전 모드 그리고 냉각 운전모드에서의 COPH&C를 분석하였으며, R134a를 적용했을 때 각 운전 모드에서 가장 높은 COP를 나타내는 것을 확인하였고, R134a를 제안된 시스템에 최적 냉매로 선정하였다.
2) R134a를 냉매로 하여 설계된 시스템을 실제로 제작하였으며, 실제 운전 조건으로 실험하기 전에 사전 실험 연구를 통해 제작된 시스템의 오작동여부를 판단하고 건조기 내부 온도 변화와 그 추이를 알아보고자 하였다. 온도 상승 운전 모드 및 냉각 운전 모드의 건조기 내부 목표 온도를 각각 25℃ 및 -5℃로 하여 구동했을 때 건조기 내부 온도의 변화가 잘 이루어지는 것을 확인하였다.
3) 설계된 실제 운전 조건으로 시스템 구동 시 건조기 내부 온도가 상온 10℃에서 목표 온도인 50℃까지 상승하는데 약 65분이 소요되었다. 운전 모드를 건조 운전 모드로 전환하고 약 200분 동안 건조기 내부 온도를 유지하였다. 연속적으로 동결 건조 모드로 전환하기 위해 건조기 내부 목표 온도를 -5℃로 하여 냉각 운전 모드를 진행하였고, 건조기 목표 온도까지 소요된 시간은 45분이었다. 연속 운전 시 모드 변화에 따른 시스템의 오작동 없이 각 모드별 건조기 내부 목표온도에 잘 도달하는 것을 확인하였고, 압축기 입구와 출구의 온도 역시 안정적으로 변화하는 것을 확인할 수 있었다.
4) 차후 연구에서는 피 건조물의 함수율 및 목표 함수율에 따른 건조 부하를 고려한 열풍 및 동결 건조용 하이브리드 히트펌프 시스템을 설계하고 최적화하는 연구를 수행할 예정이며, 건조기 내부 감압을 통해 비제습률(Specific Moisture Extraction Rate, SMER)을 향상시키는 연구 역시 수행할 예정이다.
Acknowledgments
“본 논문은 산업통상자원부 기계장비산업기술개발사업으로 지원된 연구결과입니다(연구개발 과제번호: 20018410)”.
Author contributions
J. G. Lee; Data analyzing and Writing, review & editing. C. K. Lee; Cycle simulation and Data analyzing, D. A. Cha; Conceptualization, Manufacturing, Experimental study and Supervising,
References
-
L. J. Goh et al., 2011, “Review of heat pump systems for drying application”, Renewable and Sustainable Energy Reviews, 15(9), 4788-4796.
[https://doi.org/10.1016/j.rser.2011.07.072]
-
M. Fatouh et al., 2006, “Herbs drying using a heat pump dryer”, Energy Conversion and Management, 47(15), 2629-2643.
[https://doi.org/10.1016/j.enconman.2005.10.022]
-
K. J. Chua et al., 2007, “Heat pump drying: Recent developments and future trends”, Drying technology, 20(8), 1579-1610.
[https://doi.org/10.1081/DRT-120014053]
-
M. Zielinska et al., 2013, “Microwave vacuum–assisted drying of green peas using heat pump and fluidized bed: A comparative study between atmospheric freeze drying and hot air convective drying”, Drying Technology, 31(6), 633-642.
[https://doi.org/10.1080/07373937.2012.751921]
-
D. Sun et al., 2017, “Study on combined heat pump drying with freeze‐drying of Antarctic krill and its effects on the lipids”, Journal of Food Process Engineering, 40(6), e12577.
[https://doi.org/10.1111/jfpe.12577]
-
K. Lee and O. Kim, 2009, “Investigation on drying performance and energy savings of the batch-type heat pump dryer”, Drying Technology, 27(4), 565-573.
[https://doi.org/10.1080/07373930802715708]
-
T. N. Aynur, Y. Hwang and R. Radermacher, 2010, “Integration of variable refrigerant flow and heat pump desiccant systems for the heating season”, Energy Buildings, 42(4), 468-476.
[https://doi.org/10.1016/j.enbuild.2009.10.016]
-
R. M. Lazzarina and F. Castellotti, 2007, “A new heat pump desiccant dehumidifier for supermarket application”, Energy Buildings, 39(1), 59-65.
[https://doi.org/10.1016/j.enbuild.2006.05.001]
-
T. N. Aynur, Y. Hwang and R. Radermacher, 2008, “Field performance measurements of a heat pump desiccant unit in dehumidification mode”, Energy Buildings, 40(12), 2141-2147.
[https://doi.org/10.1016/j.enbuild.2008.06.003]
-
X. Zhang, K-N. Rhee and G-J. Jung, 2020, “Simulations for the Performance Evaluation of Ground Source Heat Pump Cooling System Combined with Hot Water Heat Pump”, Journal of Power System Engineering, 24(2), 64-72.
[https://doi.org/10.9726/kspse.2020.24.2.064]
-
J. H. Moon et al., 2022, “Review for Domestic Applicability of OTEC-HP Combined Cycle”, Journal of Power System Engineering, 26(4), 81-88.
[https://doi.org/10.9726/kspse.2022.26.4.081]
-
S. T. Lim, H. J. Kim and H. S. Lee, 2016, “The Performance Analysis of Sea Water Heat Pump applied Low GWP Refrigerants”, Journal of Power System Engineering, 20(5), 92-97.
[https://doi.org/10.9726/kspse.2016.20.5.092]
-
J. I. Yoon et al., 2014, “Performance Comparison of Supercritical Heat Pump for a Variety of Refrigerants”, Journal of Power System Engineering, 18(5), 42-47.
[https://doi.org/10.9726/kspse.2014.18.5.042]
-
K. J. Bae, D. A. Cha and O. K. Kwon, 2016, “Analysis and Verification of High Temperature Heat Pump Dryer using Waste Heat Recovery Type for R245fa Refrigerant”, Journal of Power System Engineering, 20(2), 73-78.
[https://doi.org/10.9726/kspse.2016.20.2.073]
-
Y. J. Roh et al., 2022, “Numerical Analysis for the Heat and Material Balance inthe Heat Exchanger with Heat Pump”, Journal of Power System Engineering, 26(1), 49-57.
[https://doi.org/10.9726/kspse.2022.26.1.049]