
Track pin 소재용 SCr440 강봉의 최적 전단공정에 관한 연구
Abstract
The cold forming process of high strength steel rods has been widely applied in manufacturing industries. Steel rods should be effectively sheared before cold forming. The shearing behavior was investigated to obtain the optimum sheared edge quality with the SCr440 steel rod for a track pin. To determine the optimal condition the simulation program based on a finite element method was used with different cutting clearance. The sheared edge quality was evaluated by the values of roundness, rollover and inclined angle of cut surface. With the increase of cutting clearance, roundness decreased while the values of rollover and inclined angle increased. This indicates that the sheared edge quality increases with the decrease in cutting clearance. However, the decrease in clearance at less than 0.35 mm led to the significant increase in the principal stress on knife and the friction between material and dies including knife. As a result, die life decreased rapidly. The sheared edge quality as well as die life should be considered on obtaining the optimum clearance for the steel rod shearing.
Keywords:
Steel rod, Shearing clearance, Sheared-edge Quality, Die life1. 서 론
굴삭기의 하부 주행 장치의 일부인 무한궤도에 조립되는 Track pin은 현재 대부분 중국 bar 소재인 S43BC강을 구매하여 절삭 가공에 의해 제작 사용하고 있다. 그러나 S43BC강은 길이 6 m의 환봉 형태로만 수입되고 있으므로 단조 fomer에서 연속작업을 할 수 없다는 단점이 있다. 즉 각 봉의 길이가 짧아 자동다단 냉간단조(Automatic multistage cold forging(AMSCF)) 공정을 적용할 수 없어서 일일이 절삭가공을 할 수밖에 없는데, 절삭가공은 소재의 소모도 많고 제품의 기계적성질 특히 강도 등이 그다지 높지 않으며, 단조가공보다 생산성이 낮은 단점이 있다. 반면에 냉간단조는 생산성 향상과 재료절감효과가 뛰어나므로 대량생산에 주로 이용되고 있으며, 단조 시 냉간가공에 의한 강도상승 효과도 커서 제품의 신뢰도가 절삭가공에 의한 제품보다 월등히 높은 장점을 가지고 있다.
본 연구에서는 수입하고 있는 S43BC강과 기계적 특성이 유사하며, 국내에서 선재 코일 형태로 공급되기 때문에 AMSCF 공정으로 연속작업이 가능한 SCr440강을 track pin용 대체소재로 적용하기 위해 최적 절단공정을 연구하였다. 선재코일형태로 국내 생산중인 SCr440강을 track pin으로 냉간단조할 경우, 생산성이 크게 향상되어 상당한 원가절감이 예상되며 또한 수입에 따른 납기 및 가격불안정 등의 여러가지의 리스크도 회피할 수 있다. 절단다이스의 소재는 SKD11종이었으며, 이 소재는 후열처리 시 Ti 확산열처리를 행하여 표면강도 및 내마모성을 향상시켜서 많이 사용한다.1)
냉간단조에서는 가공공정, 금형의 구조, 소재의 기계적 성질, 윤활방법 등이 제품품질에 큰 영향을 주지만 단조 정밀도가 엄격해질수록 공급되는 소재의 정도도 높아지기 때문에 절단면에 대한 품질도 점점 중요시되고 있다. 특히 소재의 형상불량, 중량편차, 크랙(crack), 버어(burr) 등의 표면결함은 직접적으로 냉간 단조품의 형상, 치수 및 제품 품질을 저하시키고 금형수명 단축을 야기시키며 단조하중에 커다한 영향을 미친다.2)
대부분의 AMSCF 공정은 코일형태의 소재를 사용하고 있으며, 연속 및 자동단조 투입 전 직선으로 펴지고 전단에 의해 절단된다. 전단 시에는 단면에 결함을 발생하지 않고 경제적이어야 한다. 그러나 전단공정(shearing process) 시에는 타원형 전단표면을 포함한 전단표면의 형상결함 및 표면결함과 쇠가시(burr), 롤오버(roll over), 경사각(inclined angle) 등이 발생하기 쉽다. 최근 전단봉의 품질문제와 관련하여 절단면 품질, rollover, burr 등을 개선하기 위해 Kajino 등은2) 비틀림을 가진 전단의 새로운 복합접근방식을 제안하였으며, Behrens3)는 전단간격이 경사각, 표면결함에 미치는 연구를 수행하였다.
강봉의 경우. 전단에 의한 절단공정 시 가장 중요한 전단공정 변수는 shearing clearance(전단간격)이며, 이것은 절단 다이스와 절단 나이프 사이의 간격으로서 최적의 전단간격은 소재의 특성, 단면지름 및 quill과 knife의 형상, 전단속도 등에 의해 영향을 받는다. 아직도 많은 작업장에서는 현장 작업자의 경험에 의하여 전단조건을 정하기 때문에, 소재의 형상 및 종류에 따라 일관성이 결여되거나 표준화되지 않은 작업조건으로 작업이 행해지고 있다. 최근에는 산업현장에서 상용 유한요소 해석프로그램을 사용하여 각 절단조건에 따른 결과값을 해석하고 그 해석결과를 실제 공정에 적용하는 경우가 점차 증가하고 있다. Organ과 Mellor4)는 압축축력과 빌릿 분리 메커니즘에 중점을 두고 환봉의 절단에 대해 실험적으로 연구했으며, Liewald5)는 샌드위치 재료의 전단절단을 사용하여 카운트-전단절단 방법으로 절단 간격의 중요성을 강조했다. 그 외 Park 등6)은 자동 다단 냉간단조 장비를 사용하여 전단간격이 전단표면의 품질에 미치는 영향에 대한 실험적 연구를 수행하였으며, Moakhar 등7)은 stamping, extrusion 및 정밀단조 등의 금속성형 공정에 반제품 소재를 공급하기 전 과정인 환봉전단에 대해 연구하였다.
전단분리 작업은 단조 fomer에서 수행되었으며, 이때 좋은 절단표면을 획득해야만 이후의 성형 공정에서 결함 없이 우수한 품질의 최종제품을 생산할 수 있다. 부적절한 전단간격(shearing clearance) 에 의한 전단 작업 시에는 단면의 크랙이 발생하여 후가공 시에 edge cracking 등을 발생시킬 수 있다.8) 본 연구에서는 먼저 유한요소해석 프로그램을 이용하여 다양한 절단 간격에 따른 유효변형률 및 sheared surface 상태를 분석하고, 이 결과와 실제 AMSCF 공정을 통해 수행한 실험결과와 비교함으로써 최적의 절단면을 얻고자 하였다.
2. 재료 및 시험방법
전단간격에 따른 유효변형률을 분석하기 위해 요한요소해석법(finite element method, FEM)을 사용하였으며, 상용 소프트웨어 프로그램인 AFDEX 3D를 이용한 simulation을 실시하였다. 유한요소해석에 의해 전단간격에 따른 유효변형률을 비교하여 최적의 절단면을 얻기 위한 조건을 얻고 이를 실제 공정에 적용하여 분석하였다.
Table 1은 시험에 사용한 cold former의 제원을 나타낸다. HBF-470S Model은 4단 공정으로 구성되어 있고, Fig. 1에서는 다단 단조기에서 선재코일의 절단전 직진화(Fig. 1(a)) 및 전단공정(Fig. 1(b))을 나타내고 있다. Fig. 2는 본 연구에서 수행한 전단 공정에서 Quill, knife, stopper 및 shearing clearance의 위치를 나타내고 있다. 시험소재는 SCr 440과 S45BC 두 강종인데 두 소재의 특성을 비교하면서 기존 생산에 사용하던 S43BC강을 대체하여 SCr440강의 적용가능성을 검토하는데 주안점을 두었다. Table 2는 두 강종의 합금성분을 각각 나타내고 있는데 SCr440강의 경우, S45BC강(0.45 C%)에 비해 탄소함유량이 0.06% 더 적으며 Cr 원소가 0.86%가 첨가되어 있다.
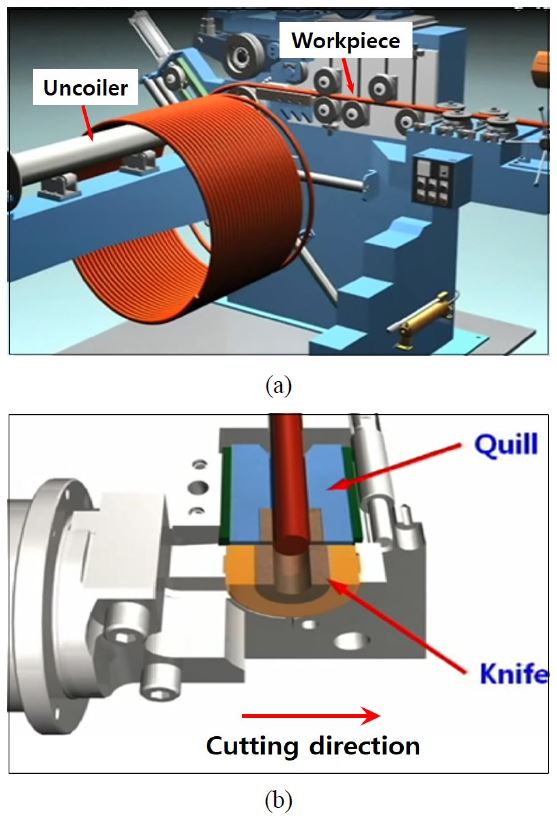
Schematic diagram of (a) shearing apparatus in automatic multistage cold forging machine and (b) shearing process
S43BC강은 B 원소를 소량 첨가하여 경화능 및 템퍼링저항성을 확보한 데 비하여, SCr440강의 경우에는 대신에 Cr 원소를 첨가함으로써 같은 특성을 획득한 것으로 생각된다. 그 외의 미량성분은 첨가량에 있어서 서로 뚜렷한 차이가 없었다. 연구에 사용된 소재는 직경이 Ø 24.20 mm인 냉간압연된 선재이다. 두 강종 모두 절단 전에는 냉간단조를 위한 구상화열처리가 행해졌다. 절단 후에는 두 강종들의 기계적 특성 및 미세조직 비교를 위해 같은 조건에서 Q-T 처리(quenching and tempering)가 수행되었으며, 이때는 870℃에서 80분간 오스테나이트화(austenitizing)하고 oil quenching한후, 450℃에서 80분간 tempering하였다. Tempering 후에는 역시 70℃에 유지된 oil bath에 급냉하였다.
인장시험은 최대하중 100 ton인 만능재료시험기(Universal Testing Machine, UTM)를 이용하여 수행하였으며, 이때 Cross head speed는 100 mm/sec로 일정하게 하였다. 각 소재의 광학현미경 미세조직 관찰을 위해 경면연마 후 수 초간 5% nital 에칭을 실시하였다.
본 연구에서는 절단면의 품질에 미치는 다른 영향을 배재하기 위해 전단 시 전단 속도(shearing speed)는 1 mm/sec로 일정하게 하였으며, 이때의 전단 하중은 0~22.6 ton의 범위에서 수행되었다. 전단간격(Shearing clearance)은 0.35~0.7 mm의 범위에서 0.05 mm씩 변화시켜 각 간격에 따른 결과를 비교하였으며, 전단간격은 Fig. 2에서 나타내는 quill과 knife의 간격을 수평으로 이동변화시킴으로써 조절하였다. 또한 절단면의 단면기울기(inclined angle) 및 눌림값(rollover)은 3차원 측정기를 사용하여 각각 3번 이상씩 측정하여 평균값을 취하였다.
3. 결과 및 고찰
3.1 소재의 미세조직과 기계적 특성
Fig. 3(a, b)에서는 구상화열처리한 보론강(S43BC)과 크롬강(SCr440)의 광학 현미경 미세조직을 관찰한 결과를 나타내고 있다. 두 강종 모두 탄화물의 구상화가 잘 이루어진 것으로 보이며, 구상화 탄화물의 밀도는 S43BC강에서 상대적으로 더 높고 탄화물의 크기도 더 미세하게 관찰되고 있다. Fig. 4는 Q-T(Quenching and tempering) 처리 후 각 강의 미세조직을 나타내고 있으며, 두 강종 모두 잘 발달된 tempered martensite 조직을 나타내고 있음을 알 수 있다. 광학현미경으로 관찰할 수 있는 범위에서 두 강종의 tempered martensite 미세조직상의 차이점은 크게 나타나지 않는다.
Table 3은 보론강(S43BC)과 크롬강(SCr440)에 대한 인장실험결과이다. 인장시험은 동일 조건에서 3회씩 시험하여 측정된 평균값이며, 표에서 보면 구상화 열처리 조건에서 S43BC강의 인장강도(Tensile strength, TS)와 항복강도(Yield strength, YS)가 SCr440강보다 뚜렷이 더 높게 나타나고 있다. 이것은 Fig. 3에서 나타내는 바와 같이 S43BC강에서 구상화 탄화물의 밀도가 상대적으로 더 높고 미세하기 때문으로 생각되며, 이것은 S43BC강의 경우, 탄소함유량이 높은 상태에서 탄화물석출을 촉진시키는 원소인 보론을 함유하였기 때문이라고 생각된다. 연신율의 경우, 구상화열처리 조건에서 SCr440강이 더 낮게 나타나고 있어서 가공성이 상대적으로 더 열악한 것으로 보이지만 항복 및 인장강도가 더 작기 때문에 소성가공에 대한 저항성이 상대적으로 크지 않을 것으로 판단된다. 또한 단조가공 시 금형 수명 확보를 위한 피단조재의 인장강도는 80 kgf/mm2 이하, 연신율은 20% 이상이어야 함을 기준으로 하고 있다는 점을 고려하면 두 강종 모두 냉간단조에 의한 소성가공이 충분히 가능한 것으로 사료된다.
Table 3에서 보면, 가공 제품의 Q-T 처리(quenching and tempering) 후 SCr440강의 강도가 S43BC강보다 상대적으로 약간 더 낮고 연신율은 더 큰 것을 알 수 있다. Q-T 처리 후의 강도를 보면 일반적으로 제품에서 요구되는 최저 항복강도값인 160 kgf/mm2보다 충분히 상회하고 있다.
3.2 전단간격에 따른 전단면 해석
상온에서 전단 시 판의 두께나 선경이 클수록 전단간격이 큰 것이 전단면의 표면품질에 유리하며,9) 선경의 강도에 따른 적정 전단간격은 연한 소재의 경우 경한 소재보다 rollover 높이 및 burr의 높이가 더 높게 발생하는 것으로 보고되고 있다.10) 이것은 전단 시 전단영역의 소성변형량과 관계가 크며 즉 판재의 두께가 두꺼울수록 소재의 강도가 약할수록 적절한 전단간격은 더 크다고 할 수 있다. 실제 공정에서 전단결함이 발생될 경우 전단표면의 불량이 최종제품 품질에 악영향을 미치게 되고, 또한 절단소재에서 발생하는 burr 또는 chip은 각 공정 금형의 수명저하까지 야기시킬 수 있다. 본 연구에서는 track pin의 절단공정에서 전단간격에 따른 전단응력 및 전단면 해석을 위해 범용적으로 사용되는 소성변형 강소성유한요소 해석프로그램인 AFDEX-3D를 사용하였다. 절단소재 및 금형은 Catia를 사용하여 360˚모델링하고 STL File로 저장하여 해석을 수행하였으며, 소재는 탄소강인 SCr440, 사이즈는 Φ26 mm×280 mm, 상온(T=20℃)이며, 금형조건에서 마찰은 Cold Normal Lubrication Hybrid(Coulomb: 0.05, constant shear: 0.1), 금형속도는 등속(Knife: -1.0 mm/s, 하형:0.0 mm/s)을 적용하였다. 전산모사 시에는 전단간격을 0.35~0.70 mm 범위에서 0.05 mm씩 변화시킨 값을 적용하여 전단 시 발생하는 유효변형률 값을 해석하였으며, 전산모사 조건과 같은 전단간격으로 실제 공정을 수행한 후 결과값을 비교 조사하였다.
Fig. 5는 전단과정을 전산모사한 그림이며, 그림의 우상부에서는 effective strain을 나타내고 있다. Quill 금형 내 변위는 Y축 방향으로 구속하였으며, knife 금형의 이동속도는 Y축 방향으로 -250 mm/s이고 quill 시작점에서 knife 종료점까지 이동시켰다.
Quill과 knife 금형조건에서 마찰은 Oil cold steel (Coulomb frictional coefficient: 0.3, constant shear friction factor: 0.6)로 적용하였고, 전단금형 내부의 구속된 요소망에서 전단방향으로 해당되는 절점에 가해지는 힘의 합(F)은 다음과 같이 가장 왼쪽 절점의 후방방향에서 선형적으로 적용한다고 가정했다.
(1) |
여기서 AE는 재료의 축방향 강성, L은 가장 우측 절단 다이스(quill) 중심에서 절단칼(knife) 가장자리까지의 길이이며 δ0는 공급롤러시스템에 의해 밀어주는 힘을 구분하기 위한 인위적인 변위, Ck는 공급시스템의 강성에 의존하는 입력전단상수 또는 전단시 압축된 재료의 좌굴효과이다. δ는 가장 왼쪽 절점의 후방변위이다. δ0와 Ck는 다양한 추측된 값에 대한 예측과 실험결과를 비교하는 매개변수 연구에 의해 결정되는 입력전단 상수이다. 구속된 요소망 절점의 측면 자유도는 모두 고정되어 있다. 전단과정에서 knife가 상부에서 하부로 이동하며 좌측의 quill은 고정되어 있고, 우측 절단면 즉 knife 측에서 burnished 영역은 Fig. 6과 같이 절단단면의 하부에 발생한다. 그림은 0.4 mm의 전단간격에서 전단시험 후 획득한 실제 전단면을 촬영한 사진이며, burnished zone과 fractured zone이 뚜렷이 구분되고 있다. 전단면은 일반적으로 rollover, burnished surface, fractured surface와 burr로 구성되어 있는데,11) 본 연구에서는 steel rod를 사용하였기 때문에 burr는 측정이 불가할 정도로 미미하게 발생하였다.
Burnished zone의 상대적인 비율을 진원도(roundness, R)라고 정의하여 R= (D-e)/D로 나타내는데, Fig. 7(a)의 그림에서 나타내는 바와 같이 e는 burnished zone의 깊이, D는 선재의 최초 지름이다. 여기서 R이 1에 가까울수록 burnished 영역이 상대적으로 작아진다는 의미가 된다. 또한 Fig. 7(b)는 절단면의 측면부에서 도시한 눌림값(rollover, t) 및 단면기울기(inclined angle, ao)를 나타내고 있다.
Fig. 8에서는 일부 전단간격(C) 범위에서 전산모사한 결과와 실제 실험 후 단면을 관찰한 결과를 비교하고 있으며, 그림에서 보면 단면에서 나타내는 fracture surface와 burnished surface의 비율이 실제 실험결과와 잘 일치하고 있음을 알 수 있다. 실제 전단 시 burnished와 fracture 영역의 상대비율은 소재의 ductile shear fracture의 함수이며, 전단 시 소재의 크기 및 기계적 특성 이외에도 적인 knife의 형상 및 특성 등에 의해 영향을 받는다. 본 연구에서는 전단간격의 변화에 따른 진원도(R), rollover (t), inclined angle (ao) 및 절단 knife 의 최대압축강도를 비교 조사하기 위해 다른 함수는 고정한 상태에서 clearance(C)만을 변화시키며 시험하였고, 그에 따라 Fig. 9의 결과를 얻을 수 있었다.
Fig. 9에서 보면, C가 클수록 진원도(R)이 감소하고, rollover 및 inclined angle이 증가하고 있는데, 이것은 이미 보고된 많은 실험 결과12-14)와 잘 일치한다. Roundness와 inclined angle의 경우 simulation 결과로는 정확히 측정할 수 없어 실제 측정치와 비교할 수 없었지만 rollover 값은 3차원 측정기를 이용한 실제 측정치(measured)와 전산모사 시 나타난 그림에서 측정한 값(simulated)을 서로 비교하여 Fig. 9(b)에서 비교하였으며, 두 결과는 거의 일치하는 결과를 나타내고 있다.
Inclined angle의 경우에는 소재의 강도가 높을수록 감소한다고 알려져 있다. 절단면의 특성에서 보면 진원도 R은 클수록 좋고 절단 봉의 후가공을 위해서는 rollover 및 inclined angle은 작을수록 우수한 단면 및 최종 단조품을 얻을 수 있다. 따라서 Fig. 9의 결과만을 가지고 최적의 C 값을 얻고자 할 때는 C가 작을수록 우수한 전단면이 구해지지만, 실제 공정에서 C가 작아지면 전단 knife 및 quill에 가해지는 하중이 증가하게 되어 전단 금형들의 수명이 감소하게 된다.
Fig. 10에서는 각각의 C에서 knife에 가해지는 주응력(prinipal stress)을 해석한 결과를 나타내고 있는데 주응력의 경우, C=0.4 mm일 때는 1,326 MPa이었다가 C=0.35 mm로 감소하면 1,489 MPa로 급격히 증가하는 것을 알 수 있다. 실제 본 연구에서 수행하였던 C가 0.4 mm 이상인 조건에서는 전단 knife의 수명이 너무 길어서 측정하기가 불가능하였다. 따라서 C=0.35 mm 이하일 때의 전단조건만을 가지고 knife의 실제 수명을 비교하여 보았는데, 그 결과를 Fig. 11 에 나타내고 있다.
Fig. 11에서 전단간격(C)이 0.35 mm에서 0.3 mm 로 감소할 때 전단 knife의 수명이 약 20만 회에서 56,000회로 급격히 저하하는 것을 알 수 있는데, 이것은 작아진 C에 의해 전단 knife에 작용하는 주응력이 급격히 상승하고 또한 절단공구와 나이프 사이의 마찰면에서 전단응력의 급상승으로 인한 마모가 심하게 발생함에 따라 나타나는 현상으로서, 실제 작업이 이루어지는 현장에서 금형수명이 급격히 저하하는 조건 즉 C=0.3 mm 이하인 조건에서 전단공정을 적용하는 것이 현실적으로 어렵다는 결론에 도달하였다. 따라서 전단공정을 위한 최적의 전단간격은 절단면과 공구의 수명을 고려할 때 0.35 mm가 가장 적당하다고 생각된다.
5. 결 론
본 연구에서는 포크레인 장비 궤도 부품인 track pin용 Bar 소재로서 기존의 보론강(S43BC)을 대신하여 냉간단조 선재인 크롬강(SCr440)의 적용 가능성을 조사하였으며, 아래의 결론을 구할 수 있었다.
1) 크롬강(SCr440)은 일반 어닐링 상태에서는 보론강(S43BC)에 비해 기계적 물성치가 낮음에도 불구하고 냉간단조 후 열처리 시 track pin에 요구되는 경도와 기계적 물성치를 확보할 수 있어서 포크레인 궤도용 소재로 적용하기에 충분하다고 생각된다.
2) 절단공정에서 전단간격(C)에 따른 절단면의 특성을 알아보기 위해 유한요소해석을 이용한 결과 C가 0.7~0.35 mm 범위에서 C가 작을수록 burnished zone, rollover와 inclined angle이 감소하여 우수한 절단면을 획득할 수 있었다.
3) 전단간격(C)은 0.70~0.35 mm의 범위에서 작을수록 우수한 절단면을 획득할 수 있는 반면에, C가 감소함에 따라 knife에 가해지는 주응력이 증가하여 전단과정에 많은 하중이 필요하게 되고 또한 knife의 수명이 급격히 감소한다. 따라서 적절한 C의 선택이 필요하며 본 연구에서는 C=0.35 mm일 때가 가장 양호하고 평탄한 절단면을 획득하였고 그보다 더 작을 경우, 금형에 가해지는 주응력이 급격히 증가함으로써 die 및 knife의 수명이 급격히 감소하여 실제 공정에 적용할 수 없다고 판단되었다.
Acknowledgments
이 논문은 부경대학교 자율창의학술연구비(2021년)에 의해 수행되었습니다.
Author contributions
K. S. Lee; Conceptualization, Data curation, Investigation. Y. S. Ahn: Methodology, Supervision, Writing-review & editing.
References
-
K. W. Nam, C. S. Kim and S. H. Ahn, 2016, "A Study on wear Damage of SKD11 Steel Material for a Cutting Mold Jig", Korean Society for Power System Engineering, Vol. 20, Issue 5, pp. 5-13.
[https://doi.org/10.9726/kspse.2016.20.5.005]
-
S. Kajino and M. Asakawa, 2020, "New billet cutting process combining torsion and shear load to reduce droop height", Journal of Materials Processing Technolog, Vol. 282.
[https://doi.org/10.1016/j.jmatprotec.2020.116660]
-
B. A. Behrens, K. Brunotte and L. Lippold, 2020, "Shearing of Aluminum Rods for the Production of Billets for Bulk Metal Forming Operations", Proc. 2nd Int. Conf. on Advances in Materials, Mechanics and Manufacturing, pp. 133-141.
[https://doi.org/10.1007/978-3-030-24247-3_15]
-
A. J. Organ, P. B. Mellor, 1967, "Some factors Affecting the Quality of Cropped Billets", International Journal of Machine Tool Design and Research, Vol. 7, Issue 4, pp. 369-389.
[https://doi.org/10.1016/0020-7357(67)90004-2]
-
M. Liewald, C. Bolay and S. Thullner, 2013, "Shear Cutting and Counter Shear Cutting of Sandwich Materials", Journal of Manufacturing Processes, Vol. 15, Issue 3, pp. 364-373.
[https://doi.org/10.1016/j.jmapro.2013.03.001]
- Y. T. Park, 2019, "A Study on Effect of Tool Clearance on Cutting Plane in Automatic Multistage Cold Forging", Thesis of Master's Degree, Gyeongsang National University.
-
S. Moakhar, H. Hentati, M. Barkallah, J. Louati, C. Bonk, B. A. Beherens and M. Haddar, 2020, "Evaluation of AW-6082 Aluminium Bar Shearing Simulation", Proc. 2nd Int. Conf. on Advances in Materials, Mechanics and Manufacturing, pp. 142-149.
[https://doi.org/10.1007/978-3-030-24247-3_16]
-
C. Hubert, L. Dubar, M. Dubar and A. Dubois, 2012, "Finite Element Simulation of the Edge-trimming/cold rolling Ssequence: Analysis of Edge Cracking", Journal of Materials Processing Technolog, Vol. 212, Issue 2, pp. 1049-1060.
[https://doi.org/10.1016/j.jmatprotec.2011.12.011]
-
Z. Tekiner, M. Nalbant and H. Gueruen, 2006, "An Experimental Study for the Effect of Different Clearances on Burr, Smooth-sheared and Blanking Force on Aluminum Sheet Metal", Materials and Design, Vol. 27, pp. 1134-1138.
[https://doi.org/10.1016/j.matdes.2005.03.013]
-
X. Wu, H. Bahmanpour and K. Schmid, 2012, "Characterization of Mechanically Sheared Edges of Dual Phase Steels", Journal of Materials Processing Technology, Vol. 212, Issue 6, pp. 1209-1224.
[https://doi.org/10.1016/j.jmatprotec.2012.01.006]
-
K. Mori, 2020, "Review of Shearing Processes of High Strength Steel Sheets", Journal of Manufacturing Materials Processing, Vol. 4, Issue 2, p. 54.
[https://doi.org/10.3390/jmmp4020054]
-
L. C. Chan, T. C. Lee, B. J. Wu and W. M. Cheung, 1998, "Experimental Study on the Shearing Behaviour of Fine-blanking versus Bar Cropping", Journal of Materials Processing Technology, Vol. 80-81, pp. 126-130.
[https://doi.org/10.1016/S0924-0136(98)00137-X]
-
Y. Chang, S. Han, X. Li, C. Wang, G. Zheng and H. Dong, 2018, "Effect of Shearing Clearance on Formability of Sheared Edge of the Third-Generation Automotive Medium-Mn Steel with Metastable Austenite", Journal of Materials Processing Technology, Vol. 259, pp. 216-227.
[https://doi.org/10.1016/j.jmatprotec.2018.04.038]
-
M. Zhoua and Y. Lia, 2019, "Investigations on Edge Quality and its Effect on Tensile Property and Fracture Patterns of QP980", Journal of Manufacturing Processes, Vol. 37, pp. 509-518.
[https://doi.org/10.1016/j.jmapro.2018.12.028]